Most of the production systems employed in clothing factories are derived from the following manual or mechanical systems. Each apparel manufacturing systems has its own specific operational characteristics. This article discusses the features, merits and demerits of different garment production systems.
Individual system/Make through/Whole garment system:
This is essentially the traditional method of production whereby one operator assembles the entire garment. In men’s bespoke wear, it is not uncommon for a tailor to perform nearly every operation required to make the garment, including machining, hand work and pressing.
With this production system the operator would be given a bundle of cut work and would proceed to sew it according to his or her own method of work. Of necessity, the labour required by this system must be highly skilled and versatile, a combination which is becoming exceedingly rare and increasingly expensive.
This type of system is effective when a very large variety of garments have to be produced in extremely small quantities. A typical application would be in the sewing room of a boutique, which produces its own merchandise.
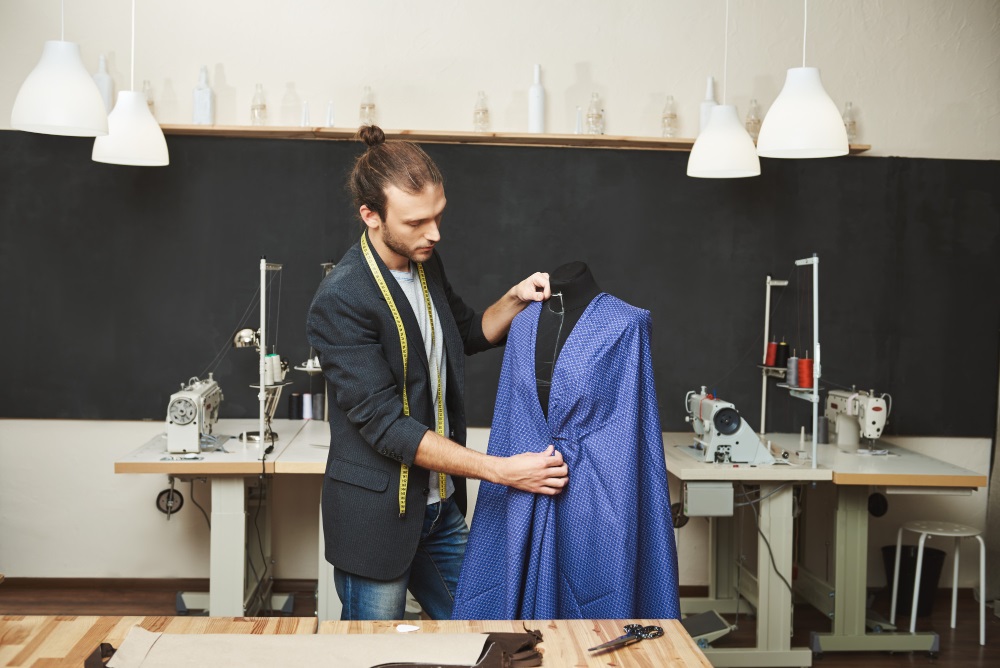
Whole Garment Production System:
There are two types of Whole Garment Production Systems:
- Complete whole garment and
- Departmental whole garment.
In the whole garment system one individual makes the entire garment from cutting the cloth to sewing and pressing the garment. The garment is ready for dispatch once the operator completes the final operation. This type of system is used in a few places, which are engaged in custom-wholesale. They are normally high priced and exclusively made for a particular customer. They are limited in number and distribution; normally about 10-20 garments are made.
The departmental whole garment system is also used by custom wholesale manufacturers as well as high price or better dress manufacturers. In the departmental whole garment system one individual does all the work with the equipment allocated to a department. For example, one person does all the cutting work in cutting department, second person does all the sewing work in sewing department, and the third person does the pressing and packing work. The workers in this system may use more than one equipment to complete their respective job.
Advantages:
1. As the labour of all levels, ie, semi skilled, skilled, trainee can be used in this system, the labour cost is less compared with individual system.
2. Productivity is higher compared to individual system, because of the use of special machine and all types of labour.
3. This system is very efficient for producing a variety of styles in reasonable quantities.
4. Automation and specialisation can be done.
5. Absenteeism and machine breakdown problems will not cause serious problems.
Disadvantages:
1. All the levels of operators are involved in the work, so the quality of garment should be strictly maintained.
2. Even though productivity is high still the highly skilled operators are required to perform simple operation within the section.
3. Group of people involved in each section and so we require more WIP, which increases the inventory cost.
4. As this is not a bundling system, there are more chances to mix up of lost, shade variation, sizes, so quality and production will be affected.
Progressive Bundle System (PBS):
This system is exactly what its name implies, a system whereby the garments are gradually assembled as they move through successive sub-assembly and main assembly operations in bundle form. The principles of this system are:
The various sections are positioned according to main operation sequence, with each section having a layout according to the sequence of operations required to produce a particular component. For example, the sleeve section could contain the following sequence of operations:
1. Run stitch collar
2. Collar turn/iron
3. Collar top stitch, etc
The amount of machinery for each operation would be determined by the output required.
A work store is positioned at the start and end of every section of these buffers is used to store work received from a preceding operation, and to hold work completed by that section.
Due to these work stores or buffers, each section is not directly dependent on the preceding section, but can absorb slight variations in output via the stocks held within the section.
The progressive bundle system, while being somewhat cumbersome in operation and requiring large quantities of work in progress, is probably one of the most stable systems as regards output. Unless there is serious absenteeism or prolonged special machine breakdowns, most of the usual hold-ups can be absorbed because of the amounts of work in progress.
Balancing and the changeover to new styles are also somewhat simplified, due to the amount of work held in reverse. When properly managed, the progressive bundle system is versatile and efficient.
Advantages:
1. Labours of all levels, ie, unskilled, skilled, semi skilled labours are involved in this system where the operations are broken into small simple operation. Hence the cost of labour is very cheap.
2. Here the quantity of each component is checked during the individual operation itself, so the quality is good.
3. The components are moved in bundles from one operation to next operation, so there is less chance for confusion like, lot mix-up, shade variation, size variation, etc.
4. Specialisation and rhythm of operation increase productivity.
5. As the WIP is high in this system, this is stable system. Because of the buffer, the breakdown, absenteeism, balancing of line, change of style can be easily managed.
6. An effective production control system and quality control system can be implemented.
a. Time study, method study techniques.
b. Operator training programme.
c. Use of material handling equipment, such as centre table, chute, conveyor, trolley, bins, etc. 7. Bundle tracking is possible, so identifying and solving the problems becomes easy.
Disadvantages:
1. Balancing the line is difficult and this problem is solved by an efficient supervisor.
2. Proper maintenance of equipment and machinery is needed.
3. Proper planning requires for each batch and for each style, which takes a lot of time.
4. Improper planning causes labour turnover, poor quality, less production, etc.
5. Increase in WIP in each section increases the inventory cost.
6. Planned and proper layout should be made to make the system effective, ie, smooth flow of material.
7. Variety of styles & less quantity are not effective in this system.
8. Shuttle operators and utility operators needed in every batch to balance the line effectively.
Straight-line or ‘Synchro’ System:
As its name suggests, this system is based on a synchronised flow of work through each stage of producing a garment. Time-synchronisation is the most important factor of this system because the flow of work cannot be synchronised if there are considerable variations in the standard times allowed for all the operations performed on the line.
For example, if one operation has a value of 1.5 minutes SAM, then all the other operations in the line must have the same, or a very close, value. The manipulation required to balance the standard time for each operator can sometimes lead to illogical combinations of whole or part operations which are not always conducive to the overall efficiency of individual operators.
Unit Production System (UPS):
As a mechanical system this has been in use for many years, but a major advance was made in 1983 when computers were first used to plan, control and direct the flow of work through the system.
Features:
1. The unit of production is a single garment and not bundles.
2. The garment components are automatically transported from workstation to work station according to a pre-determined sequence.
3. The work stations are so constructed that the components are presented as close as possible to the operator’s left hand in order to reduce the amount of movement required to grasp and position and component to be sewn.
The operational principles:
All the components for one garment are loaded into a carrier at a workstation specially designed for this purpose. The carrier itself is divided into sections, with each section having a quick-release clamp, which prevents the components from falling out during movement through the system. When a batch of garments has been loaded into carriers they are fed past a mechanical or electronic device, which records the number of the carrier and addresses it to its first destination. Some of the more intelligent systems address the carriers with all the destinations they will have to pass through to completion.
The loaded carriers are then fed onto the main powered line, which continually circulates between the rows of machines. This main, or head, line is connected to each workstation by junctions, which open automatically if the work on a carrier is addressed to that particular station. The carrier is directed to the left side of the operator and waits its turn along with the other carriers in the station.
When the operator has completed work on one carrier, a push button at the side of the sewing machine is pressed and this actuates a mechanism, which transports the carrier back to the main line. As one carrier leaves the station, another is automatically fed in to take its place. When the carrier leaves the station it is recorded on the data collection system, and then addressed to its next destination.
Unit Production System requires substantial investments, which are not always justified by conventional payback calculations. Apart from the measurable tangible benefits, UPS also have many intangible benefits such as a more orderly and controlled flow of work, and the ability via the control computer of simulating the production situation some time in advance. These intangibles are difficult to measure, but in themselves make a very positive contribution to the overall viability of the unit.
All things considered, unit production systems have major advantages over all the other manual and the mechanical systems used for the mass production of clothing. Most importantly, they provide a clothing factory with the capability to respond quickly to any changes, which might occur. In the fast moving fashion business, this is essential.
Advantages:
1. Bundle handling completely eliminated.
2. The time involved in the pick-up and disposal is reduced to minimum.
3. Output is automatically recorded, eliminates the operator to register the work.
4. The computerised systems automatically balance the work between stations.
5. Up to 40 styles can be produced simultaneously on one system.
Disadvantages:
1. Unit production system requires high investments.
2. The payback period of the investment takes long time.
3. Proper planning is required to be effective.
Quick Response Sewing System:
This system was first developed in Japan to enable quick responses to be made to market changes, especially when orders for individual styles were in small lots. Each workstation is equipped with two or four machines and the operator will take the garment through the required operations, including pressing, before it is transported to the next workstation.
Layout:
Some of the basic machinery is duplicated in different stations and if there is a bottleneck in one section the overload is automatically transported to other stations where operator capacity is available.
All the parts of one garment are loaded into a hanging clamp attached to the trolley and in theory, there should only be one garment at each workstation. Work is transported by a computer controlled, overhead trolley system and each station has an individual controller, which provides the operator with information on the style being worked on. This information comes from an information card, which accompanies each trolley.
A less sophisticated version of QRS uses a wheeled trolley, which contains the components for one garment and is pushed along the floor from operator to operator.
Another feature of QRS is that all the operators work in a standing position so that they can move quickly from one machine to another within their own workstation. Machine heights are adjusted accordingly and touch-pads and knee-pads controls are used instead of conventional foot pedals.
Features:
- Supervision: Freed to work with the operators.
- Labour: Of necessity the operators must be highly skilled in the operation of all the different machines in one workstation.
- Quality: In-process inspection stations are built into the line and the inspector is able to return faulty work via the system to the operator concerned.
- Productivity: This is very high because the operator handles the garment once only for a number of operations, instead of once for each operation.
- Throughput time: As there are so few garments on the line throughput time is extremely short, which is the objective of this system.
- Layout: A typical unit would have eight work stations arranges around the transport system.
Modular Apparel Manufacturing system(TPS):
A modular garments production system is a contained, manageable work unit that includes an empowered work team, equipment, and work to be executed. Modules frequently operate as mini-factories with teams responsible for group goals and self-management. The number of teams in a plant varies with the size and needs of the firm and product line in garments. Teams can have a niche function as long as there are orders for that type of garments product, but the success of this type of garments operation is in the flexibility of being able to produce a wide variety of products in small quantities in garments.
Many different names are currently used to identify modular garments production systems, including modular garments manufacturing, cellular garments manufacturing units, compact work teams, flexible work groups, self-directed work teams, and Toyota Sewing System (TSS) in garments. The basic premise is similar among these production systems, although the organization and implementation may vary.
The number of employees on a team, usually 4 to 15, varies with the product mix. A general rule of thumb is to determine the average number of operations required for a style being produced and divide by three. Team members cross-trained and interchangeable among tasks within the group. Incentive compensation is based on group pay and bonuses for meeting team goals for output and quality. Individual incentive compensation is not appropriate for team-based garments production. Teams may be used to perform all the operations or a certain portion of the assembly operations depending on the organization of the module and processes required. Before a firm can establish a modular production system, it must prioritize its goals and make decisions that reflect the needs of the firm.
With a team-based system operators are given the responsibility for operating their module to meet goals for throughput and quality. The team is responsible for maintaining a smooth work flow, meeting production goals, maintaining a specified quality level, and handling motivational support for the team. Team members develop an interdependency to improve the process and accomplish their goals. Interdependency is the relationship among team members that utilizes everyone’s strengths for the betterment of the team.
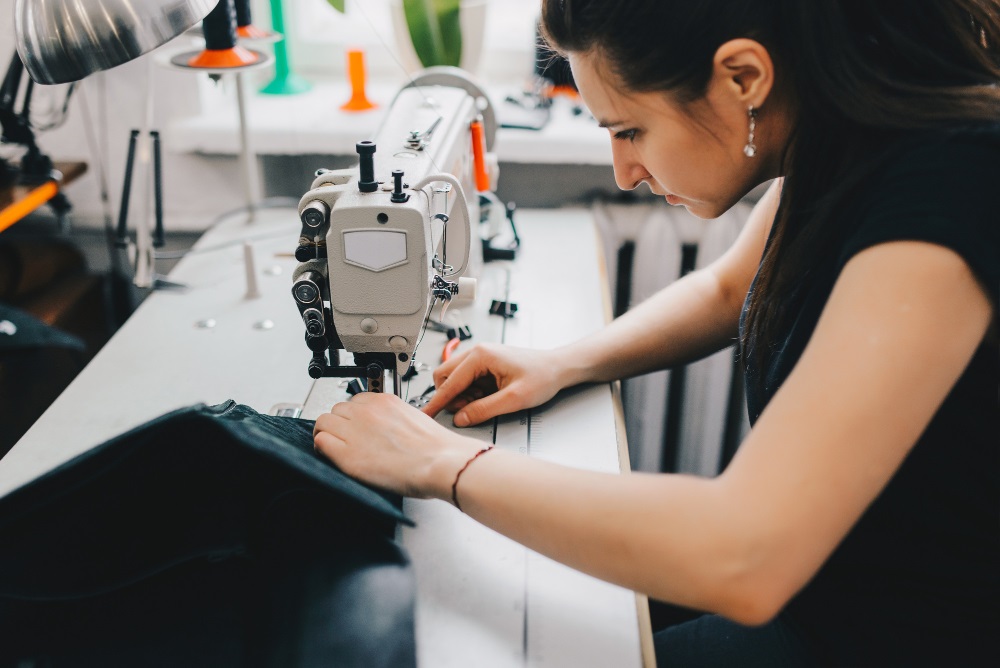
Workflow in modular garments production:
A Modular garments Production System operates as a Pull System, with demand for work coming from the next operator in line to process the garment. Wastage is normal, and workflow is continuous and does not wait ahead of each operation. This increases the potentials for flexibility of styles and quantities of products that can be produced. Teams usually operate as ‘Stand-up’ or ‘Sit-down’ units.
A module may be divided into several work zones based on the sequence of garments operations and the time required for each operation. A work zone consists of a group of sequential garment operations. Operators are trained to perform the operations in their work zone and adjacent operations in adjoining work zones so they can move freely from one operation to another as the garment progresses.
Workflow within a module may be with a Single-piece hand-off, Kanban, or Bump-back system. If a single-piece hand-off is used, machines are arranged in a very tight configuration. As soon as an operation is completed the part is handed to the next operator for processing. Operations need to be well balanced as there is usually only one garment component between each operation. Some modules may operate with a buffer or small bundle of up to ten pieces of work between operators. If a small bundle is used, an operator will complete the operation on the entire bundle and carry the bundle to the next operation. An operator may follow a component or bundle for as many operations as they have been trained or until the adjacent operator is ready to assume work on the bundle.
A Kanban uses a designated work space between operations to balance supply with demand. The designated space will hold a limited number of completed components (two or three) in queue for the next operation. If the designated space is full, there is no need to produce more until it is needed or the space empties. This limits the build-up of products ahead of the next operation. When the space is full the operator can assist with other operations that may be slow.
The bump-back or TSS (Toyota Sewing System) approach was developed by the Toyota Sewn Product Management System and is probably the most widely used type of team-based manufacturing. It is a stand-up module with flexible work zones and cross-trained operators. Operators may be cross-trained on up to four different successive operations. This enables operators to shift from operation to operation until the next operator is ready to begin work on the garment. The operator needing work steps to the beginning of the zone and takes over the processing at whatever point it is in the production process. The operator who has been relieved of the garment will then move back to the beginning of the work zone and take over work on another garment. This approach enables continuous work on a garment and allows each operator to perform several different operations. This arrangement frequently uses a 4-to-l ratio of machines to operators.
The advantages of a Modular Garment Production System are:
1.) High flexibility
2.) Fast throughput times
3.) Low wastages
4.) Reduced Absenteeism
5.) Reduced Repetitive Motion Ailments
6.) Increased employee ownership of the production process
7.) Empowered employees
8.) Improved Quality
Disadvantages of Modular Garments Production System:
1.) A high capital investment in equipment.
2.) High investment in initial training.
3.) High cost incurred in continued training
References:
http://www.indiantextilejournal.com
http://fibres2fabrics.blogspot.com
Image by freepic.diller on Freepik
Image by prostooleh on Freepik
Image by cookie_studio on Freepik