What is Lean Manufacturing?
Lean manufacturing is a systematic approach to identify and eliminate wastes(Muda:-non-value added activities) through continuous improvement by conveying the product at the pull of the customer in pursuit of production. In a more basic term, more value with less work.
This is the manufacturing system developed by Toyota which pursues optimum streamlining throughout the entire system through the elimination of Muda (non-value added activities) and aims to build quality in at the manufacturing process while recognizing the principle of cost reduction. It also includes all the accompanying technology necessary to accomplish those aims. The two main sub-systems supporting the Toyota Production System are “Just-In-Time” and “Jidoka.”
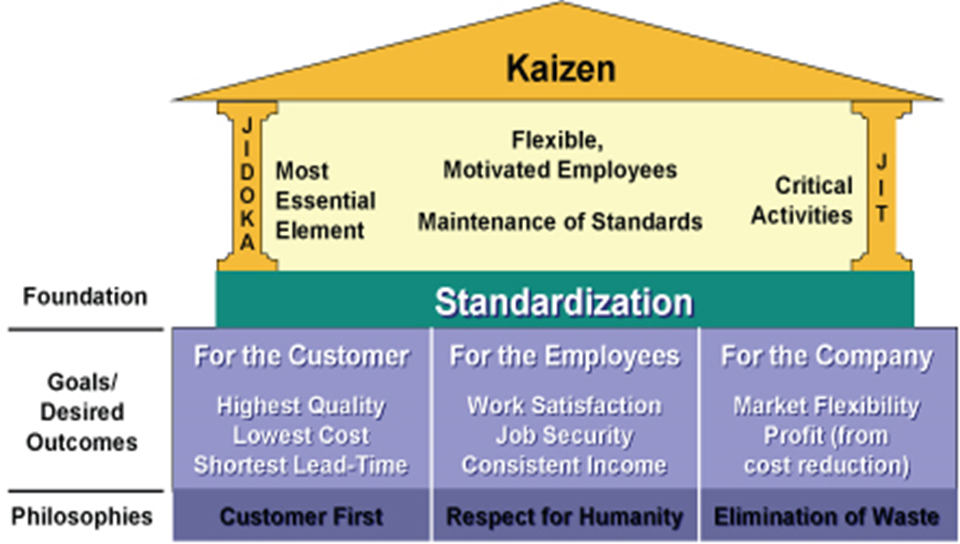
Kaizen:
Muda (non-value added) exist everywhere related to people, material and facilities, or the production set-up itself. Kaizen refers to the series of activities whereby instances of Muda are eliminated one by one at minimal cost, by workers pooling their wisdom and increasing efficiency in a timely manner. Kaizen activities typically emphasize manual work operations rather than equipment. Also, Kaizen is not an activity to be performed by a specialist, but can be in fact should be performed by all employees at each job site.
Muda:
Muda (non-value added – usually translated as waste) refers to those elements of production that add no value to the product and only raise costs:
- Muda of Over-Production
- Muda of Waiting
- Muda of Conveyance
- Muda in Processing
- Muda in Inventory
- Muda of Motion
- Muda of Correction
Muda of Over Production:
Just-In-Time production is an ironclad rule at Toyota and producing anything 1) earlier than needed or 2) in greater volumes than needed (as indicated by kanban or other indicators) results in excess inventory and is known as muda or over production. This muda often hides muda of waiting and muda of motion. It also leads to muda by an increase in the number of conveyance vehicles and pallets. Among the different kinds of muda, muda of over-production is the most serious.
Muda of Waiting:
This refers to a situation where a worker who has been working according to a standardized work sequence finds himself unable to process to the next job. This often occurs due to the volume of work being low.
Muda of Over Transport:
Conveyance itself is basically muda since it doesn’t add any value to the product: the more conveyance per unit, the more the final product cost. This term refers to any conveyance above the minimum necessary to keep “Juts-In-Time” production operating smoothly – such as temporary unloading, load transfer, removal of small quantities, and movement from one spot to another.
Muda in Processing:
Any work or processing that does not add value to the product and advance the production process or contribute to the precision or quality of the processed units is referred to as Muda in Processing.
Muda in Inventory:
All of the inventory (materials in-process work and finished products) that derives from the process of production and conveyance.
Muda of Motion:
Muda of Motion is any human movement in production that adds no value to the product.
Muda of Correction:
This refers to the muda of producing defective items which must be repaired or discarded. Includes the regular processes which tend to make people less aware of the muda involved and therefore impair improvement.
Jidoka:
It refers to the ability of production lines to be stopped in the event of such problems as equipment malfunctions, quality problems or work being late either using machines which have the ability to sense abnormalities or using workers who push a line-stop button. This prevents passing on defects. Reoccurrence prevention becomes simpler as abnormalities become more obvious making it possible to “build in quality at the production process”.At the same time, since defects are prevented automatically, inspectors become unnecessary, which in turn results in significant labor savings.
Just-In-Time:
One of the two pillars of the Toyota Production System, Just-In-Time refers to the manufacturing and conveyance of only what is needed, in the amount needed. This enhances efficiency and enables quick responses to change.
My Opinion regarding LEAN MANUFACTURING:
The lean theory may sound very complex but the knowledge it gives will be basic and very practical for a learned individual. People should find lean to be easy to understand and implement rather than seeing it as a complex animal.
Though there is some problems, The only required things to implement Lean Manufacturing in Apparel Industry is now the willingness of the top management.
Ref. :