Compacting is a textile finishing machine specifically designed for compacting 100% cotton knitted fabrics such as jersey, pique, interlock, and rib. Compactors are also called compactors or felt compactors. The purpose of the compacting machine is to prevent the shrinkage of knitwear. Compression can be done not only on tubular fabrics but also on wide fabrics. Residual shrinkage of the fabric can be reduced from 3% up to 0%. In addition to residual shrinkage, GSM is also checked.
There are two types of compacting machines:
- Tubular machines
- Open Width machines
Tubular compactor machine:
A tubular compactor machine is used as a finishing machine for tubular knitted fabrics. Tubular compactor machines are used for shrinkage control, GSM control, and increased smoothness of fabric. A Tubular compactor is an industrial machine used after hydro-extractor, dewatering, and dryer. This machine is installed after the industrial dryer.
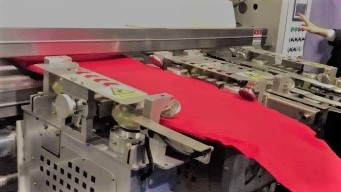
Functions of Tubular Compactor:
- Fabric shrinkage is controlled by a tubular compactor.
- The width of the fabric is controlled by a tubular compactor.
- The basis weight of the fabric is adjusted by a tubular compactor.
- The smoothness of the fabric is achieved by a tubular compactor.
- Heat setting of Lycra fabric is done using a tubular compactor.
Open Width compactor machines:
Open-width compactors are used to compact open foam webs. Here a slitting machine is used to cut open the tubular fabric. Open width compacting machine is a combination machine of pin plate stenter and felt compactor and is used to process 100% cotton, wool, natural linen fabric, chemical fiber, etc. into an open-width shape.
Functions of Open Width Compacting Machine:
- To finish the fabric
- To compact the fabric
- To control shrinkage
- fabric diameter control
- Maintain to get proper width and G.S.M.
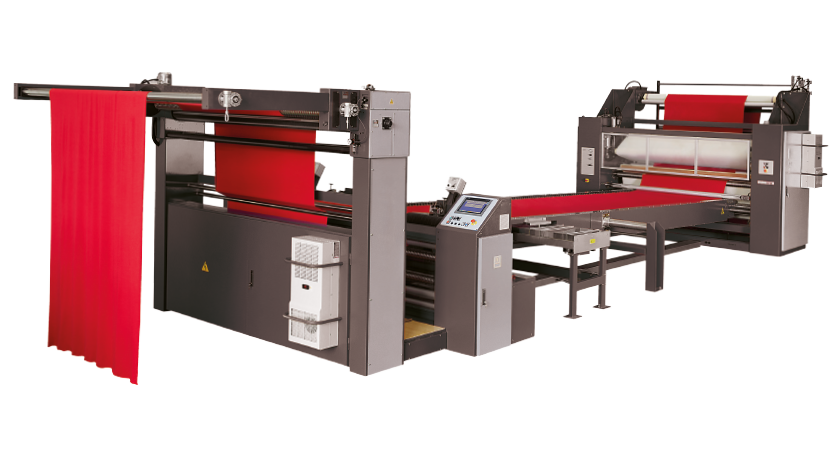
Elements of Compacting Machine in Textile Finishing:
A compactor machine has an entry, a small tenter frame, a steaming unit, and a set of felt and rollers. It has J Box or rolling at the exit. There are also Compactors with metal shoes.
The fault of the Compactor machine:
- Teflon problem
- Tension bar problem
- J-box Compensator problem
- Blanket moving problem
- Steam and Air problem
- Cooling Motor Fan problem and so on
Checklist Before starting Production in Compactor machine:
Before the finishing, re-finishing, heat setting, and stretching processes in the compactor machine, the operator should ensure the following things:
● Check the program with fabric specification
● Make sure the required manpower is available for the feed side and delivery side.
● Feed side fabric is ready.
● Check machine parameters are set.
Checking Parameters of Compactor Machine:
Following parameters check in the compactor machine.
1. Shade Check: The shade of the compacting fabric is checked at the delivery side of the machine. The operator collects the fabric and compares the shade of the fabric to the buyer-approved sample.
2. Width Check: The operator measures the width of the fabric with a tape measure and compares it with the buyer’s request.
3. Weight Check: The GSM check determines the fabric’s weight. The fabric’s GSM is checked by the operator using an electric balance and GSM cutter.
4. Edge Line Checking: Verify the fabric’s two delivery-side edges. It should be fixed if any fixed lines are found, which often come from the expander wheel.
5. Fault Check: The delivery side of the fabric is where many fabric qualities are measured.
Ref.:
- https://textilelearner.net
- Photo by Ron Lach : https://www.pexels.com