The standardization of colour measurement is essential to control and achieve accurate colour communication.
A set of procedures for colour measurement has been created to minimize error. These procedures will also help to achieve greater consistency of shade in stores whilst eliminating delays, therefore reducing lead times and increasing flexibility.
Equipment Required:
1. Conditioning Cabinet
All fabrics must be conditioned prior to measurement to eliminate any colour changes caused by changes in temperature, moisture content and to a lesser extent exposure to light. Conditioning for 30 minutes in a rapid conditioning unit is recommended with the following settings:
- 20°C ± 2°C temperature
- 65% ± 2% relative humidity
- D65 lighting.
Conditioning for one hour is also acceptable, however the above method is preferred. Different Brands recommend different conditioning time. But mostly followed above.
All samples must be conditioned from a dry state.
It is critical that readings should be taken within 5 minutes of removal from the conditioned atmosphere. Fabrics should be kept in a plastic container whilst being transported to eliminate changes in moisture content prior to measurement. We would advise that the conditioning cabinet is in the same place as where the measurement is taking place.
We recommends the use of a Vindon Ultrasonic Humidity Cabinet which is suitable for conditioning samples under the required temperature, humidity and illumination for 30 minutes.
Light Box
All light boxes used for assessing colour must be re-painted on a yearly basis. The wall area of the cabinet should be finished in light grey emulsion; the colour specified is Munsel N5. Different Brands recommend different lightbox for color assessment.
The lights must be changed every 2000 hours or annually, whichever comes first.
Spectrophotometer
The following settings for the spectrophotometer are required for one of the specific brands, it could be changed a bit for for any other brand:
- Spectrophotometer – Once switched on the spectrophotometer should be allowed to warm up over 30 minutes prior to calibrating the machine or making any measurements
- Calibration – The spectrophotometer should be calibrated at least every 8 hours
- Observer Weighting – 10° is recommended as this gives better correlation with practical visual assessment than 2°
- Aperture Size – The largest aperture size possible should always be used for a more accurate measurement
- Fabric Direction – Fabrics should be rotated between readings. Textile fabrics are never completely uniform so moving the sample in between each reading helps to even out any difference in dyeing and gives more reproducible measurements
- Number of Readings Taken – For the most reproducible measurements between different operatives a minimum of 4 readings should be taken and the fabric rotated in 90 degrees between each reading. The average of these readings will automatically be given by the spectrophotometer. For polar fleeces and other pile fabrics the number of readings will need to be increased to 5
- Thickness of Fabric – At least 4 layers of fabric should be used, or enough so that the sample is fully opaque. The number of layers will determine the sample size required to obtain an accurate measurement. For a reading using 4 layers of fabric and the largest aperture, a sample size of approximately 25cm x 10cm will be required
- Background Colour – For sheer fabrics or where there is not enough fabric to fold, a similar colour background to the fabric should be used. Please check that any background colours used do not contain UV. This minimizes any inaccuracies caused by light reflecting off the back of the holder and adding to the colour reading
Method for Spectrophotometer Measurement:
Apparatus:
- A reflectance Spectrophotometer measuring every 10 nanometers is required which needs to be fully compatible with the Spectraflash 800 (used by one specific Brand).
- A rapid conditioning cabinet or conditioned laboratory
Instrument Set Up:
The following settings are required for correlated colour measurement:
- CMC 2:1 colour difference equation
- Specular Component Included (SCI)
- UV included (UVI)
- Large Aperture Viewing (LAV) ~ the largest aperture should be used wherever possible, otherwise use the maximum size possible to fit the sample
- 10° observer
- The Spectrophotometer should be set to take an average of 4 readings
- D65, Artificial Daylight is used as the standard illuminant for specific Brand.
F11 (TL84) should be used as a secondary illuminant and Tungsten as the tertiary illuminant to check for metamerism
Method for Measuring Plain Fabrics:
- The fabric sample should be folded enough times so that light cannot be transmitted through the sample (i.e. when the folded sample is put over a piece of similar coloured paper placed side by side, the line between the two pieces of paper cannot be seen). A minimum of 4 layers are recommended however the sample should not be so thick as to protrude into the measuring sphere
- The sample should be smooth, without creases, staple holes or any contamination. Place the sample against the measuring port and check that a smooth surface has been presented for measurement. (The warp should always be vertically aligned)
- Take a reflectance measurement
- Rotate the fabric 90 degrees (repeat step 3)
- Rotate the fabric 90 degrees (repeat step 3)
- Rotate the fabric 90 degrees (repeat step 3)
- The average of the 4 readings will automatically be given
Method for Measuring Pile Fabrics:
When measuring substrates with a pronounced texture, it is imperative that the following method is followed. Significant variation in measurements can result, depending on pile direction and the degree of rotation during measurement. To obtain the most accurate reading it is essential that the Large Aperture Viewing (LAV) is used and all fabrics should be in a conditioned state prior to measurement.
In this category we would also include fabrics which have a surface direction which could affect the shade, for example suedette and fleece.
Measuring with Directional Pile:
- A minimum of 4 layers are required to give an accurate measurement for suedette, or single layer of fleece (ensure that the fabric is folded enough times to be fully opaque)
- Brush surface of suedette / fleece down so all fibres are flat and are orientated in the same direction as the pile
- Take the first measurement with the pile facing down
- Remove and re-brush the suedette / fleece in the same direction as the pile
- Rotate the fabric 72 degrees clockwise (This movement is critical) and present to spectrophotometer in new position. Take measurement
- Repeat steps 4, 5 and 6 until 5 measurements have been taken (fabric rotated through 360 degrees)
- Accept these measurements and the average value will automatically be calculated
Instrumental Colour Measurement of Whites:
Methods and Procedures:
Spectrophotometers should be characterised for white measurement according to manufacturer’s recommendations and in some cases may require a manual modification of the machine set-up. The UV tile should be re-checked against the Hohenstein Whiteness values at time of annual accreditation. When dyeing white on a regular bases UV Calibration must be carried out weekly. If dyeing white occasionally UV Calibration should be actioned at time of measuring. Readings from machines that have not been characterised for UV content will not be accepted.
The CIE whiteness equation should be selected. This equation gives two figures:
- A whiteness value (100 is a perfect white without the use of optical brightening agents)
- A tint value (indicating whether the white has a red or green coloured tinge)
The equation gives a reading in simulated D65 light. This light contains more UV light than F11 (TL84 Store Light) so the figures can look better than reality if a dyer has used large amounts of optical brightening agent on a poorly prepared, non-white base. To check the dyer has achieved a good white under the optical brightener a reading should be taken without UV. CIE Whiteness units are used as a guideline to the degree of whiteness required. As fabric construction has a direct influence on light reflectance, measured values should always be used in conjunction with visual assessment.
Visual white standards must be renewed every 6 months and should be stored in a clean dark area, for example a drawer.
Example of Whiteness Printout:
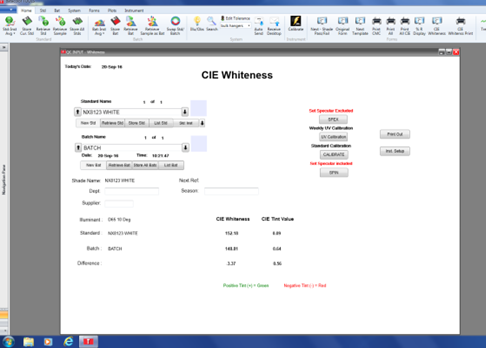
Ref.: Image from https://www.datacolor.com.