Textile printing is an intriguing process that enhances fabrics with vibrant colors and captivating designs. Screen printing is a common method where inks are applied directly to the fabric, whereas it offers a distinct approach to achieving impressive results. Discharge printing is a method where a chemical agent is applied to the dyed fabric to remove (or discharge) the color from that specific area. This process creates a distinctive design by either revealing the original fabric color or replacing the previous dye with a new color. Simply, it’s a subtractive method of printing that takes away color instead of adding it.
Types of Discharge printing:
- White Discharge Printing: In this method, the color is taken out from the dyed fabric, which creates patterns in white or almost white shades.
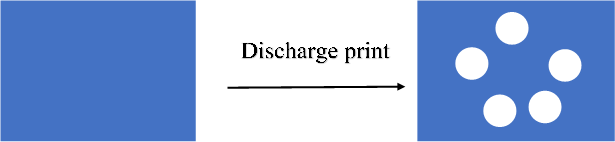
- Colored Discharge Printing: During this process, the original dye is removed and a new color is added at the same time, allowing for a colorful design on a pre-dyed fabric.
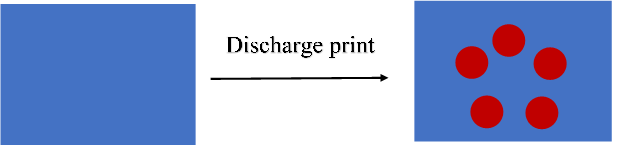
Process of Discharge Printing:
- Fabric Preparation: The fabric commonly made from natural fibers like cotton, is dyed with a color that can be discharged. Reactive or vat dyes are often preferred since they can be easily discharged by discharging agents.
- Screen Preparation: A stencil or screen is initially prepared with the desired design. Then the discharge paste, containing special chemicals is applied through this screen onto the fabric.
- Chemical Application: The discharge paste contains reducing agents like Zinc formaldehyde sulfoxylate that remove color from the dyed fabric by breaking down dye molecules in printed areas.
- Curing: Then the fabric is cured after the paste is applied to fully activate the discharge agents at 190ºC for around 2-3 mins, with the heat accelerating the chemical reactions to ensure complete removal of the dye. Depending on the size of the dryer or fabric we may need to adjust the parameters.
- Washing and Finishing: After the discharge process is completed, the fabric is washed to remove the chemicals and dye particles to prevent any damage to the fabric and ensuring a sharp design. It is then dried and ready for use.
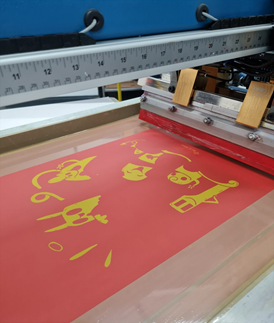
Types of fabrics for discharging Printing:
To ensure the process works well, the fabric needs to be dyed with a dischargeable dye. Not all dyes can be discharged, so not all fabrics are suitable for It. The most common fabric used in this process is cotton, particularly dark-colored cotton because the dark color allows for a stark contrast with the vibrant colors of discharge ink. Synthetic fabrics like polyester and nylon are not ideal for discharge printing because their dyes cannot be discharged. Likewise, fabrics that are dyed with vat dyes or reactive dyes may not respond well to discharge techniques.
Application of Discharge Printing:
Fashion industry: Luxury brands often use discharge printing to create floral or geometric designs on silk scarves or high-end cotton shirts. This technique is also used in more casual clothing such as t-shirts and hoodies.
Home Textiles: It is used to create elaborate designs on bed linens such as duvet covers and pillowcases. Curtains and upholstery often also use this technique to achieve sophisticated and elegant designs. Moreover, several limited edition and custom items use discharge printing which offers more personalized and distinctive designs.
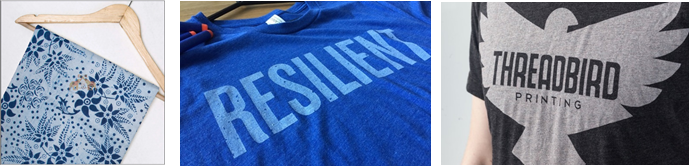
It is a more complex process compared to other printing because it needs precise temperature control and careful handling to achieve a consistent result. Due to its complexity and specialized equipment requirements, discharge printing tends to have higher cost than other techniques. It eliminates the need for separate dye baths and reduces overall water consumption making it a more sustainable production practice though the process involves the use of chemicals that need to be managed properly. So, while the process has its challenges, including environmental concerns and complexity, its benefits of producing sharp, soft, and versatile prints make it a valuable printing process.
References:
- https://en.wikipedia.org/wiki/Discharge_printing
- https://www.mondaymerch.com/resources/printing-techniques/discharge-ink-printing-techniques-explained
- https://www.magnacolours.com/discharge-printing-a-step-by-step-guide/
- https://www.extremescreenprints.com/post/a-deep-dive-into-discharge-screen-printing