Material Required for Screen Printing :
So many materials are required during screen printing. below are few among them….
- Printing Table
- Screens
- Bed on printing table
- Back grey
- Fabric to be printed
- Squeezer
- Drying and curing zone
- Washing zone
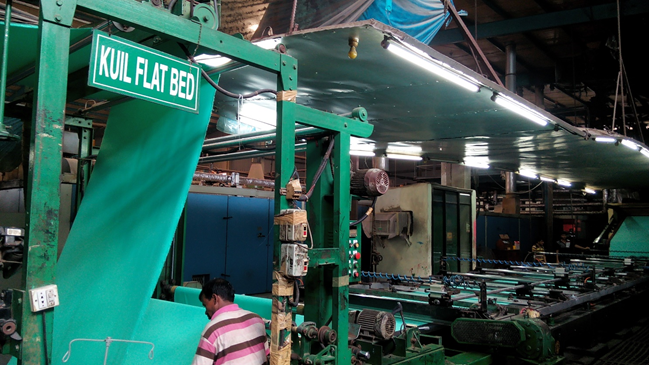
Steps before making all over screen printing with machine are described below….
-
DESING SELECTION:
Design is created on a film or paper in the design room by operator according to the buyer’s requirement. Adobe illustrator software is used while creating design.
-
SCREEN PREPARATION:
Normally the silk screen and rotary screen are coated with photo-emulsion containing photo sensitizer. By coating the compound over the screen with a very thick film on the screen, the screen is allowed to be dried in room temperature without light. The master design will be produced by using black color covering the areas that needed the ink to pass through. Using a light bulb table the design will transfer from the master design to the screen by exposing it to light for 2-5 mins. After that, the screen is washed and dried. Operators often sharpen the screen using needles in case of any faults being present.
Screen Preparation area
3. PRINT PASTE PREPARATION:
The mail chemical used for print paste as below.
- Thickener
- Binder
- Fixing agent
- Oxgel (leveling agent)
- Urea
- Ammonia liquor for no jamming on screen
4. Printing :
— The fabric (woven or knit) to be printed is feed to the blanket at the entry zone and is welded by glue with endless conveyor belt.
— The conveyor draws forward below screen in equal difference and printing paste, mechanically supplied, is welded on fabric according to design by squeezing through screen.
— Six different colors can be used by six screens and printing effect of different colors can be brought.
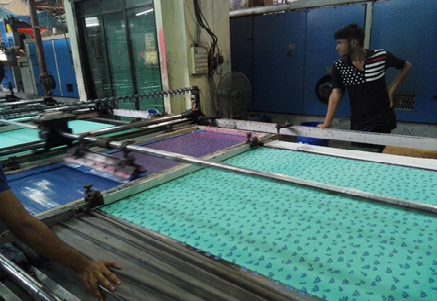
-
DRYING AND CURING:
In this machine, generally the fabric is printed with pigment of reactive dyes.
— After printing, drying is necessary for both pigment and reactive dyes.
— For pigment printing, curing is done at 180°C.
-
WASHING:
Pigment printing- No wash
Reactive – wash (for good fastness property)
Controlling points of Screen All Over Print:
- The mesh (thread/inch) of screen should be notified because a coarse mesh allows more paste to pass through than a fine one.
- The viscosity of the print paste.
- The number of squeeze strokes.
- The sharpness of the screen design.
- For pigment printing, curing temperature should not be less than 180°C.
Ref. :
- Based on “Industrial Attachment on Asian Textiles Mills Ltd” by Fatema Akter, Md. Kamrul islam, Jishan Ahmed &Al-Amin under supervision of Kawser Parveen Chowdhury, Lecturer, Department of wet Processing Engineering, Bangladesh University of Textiles.