Apparel manufacturing includes number of processes from order receiving to dispatching shipment of the finished garments [1]. The term apparel finishing is an important part of garment manufacturing mainly applies to pressing, folding and packing of garments [2]. It covers all the operations required to complete a garment. For most garments, this process starts after pressing. The details involved in finishing vary according to garment type [3].
Developments in Apparel Pressing Machine:
In the high-volume clothing manufacturing industry, pressing is the final production stage and as such follows garment design, fabric cutting and making-up. The pressing process is used extensively throughout the clothing industry, both in garment production units and in the aftercare processes of laundering and dry cleaning. The reasons for this are largely commercial, as pressing can be used to noticeably improve the appearance of clothing by removing unwanted creases and handling marks created during manufacture. Having thus restored a smooth outer surface to the item, this enhanced appearance makes the garment more attractive to prospective customers. The handle and the feel of clothing can also be improved by using a finishing process [4] to remove the glaze on a fabric by raising the nap of the constituent textile material; even though little pressure may be applied, such processes are still known as ‘pressing’ [5], which tends to be used as an all-encompassing term. The pressing process conventionally involves the application of heat, moisture (normally in the form of steam) and pressure, either individually or in combination [6]
The Smoothing Iron:
The most common type of iron in general use is the steam electric. The iron is heated by an electric element, controlled by a thermostat, and supplied with steam, either from the factory’s main steam supply, or from a small boiler adjacent to the pressing unit. The steam function of the iron is activated by the touch of a button, when a powerful jet of dry steam is produced. At extremes, the weights of irons vary from about 2–15 kilos. Several shapes are available including a roughly triangular one similar to a domestic iron, the ‘tailor’s shape’ which has a
pointed nose and parallel sides, and a narrow one used for operations such as seam opening on sleeves and trouser legs. There is a range of workplaces available for ironing. In a situation where a variety of parts and shapes of garments has to be pressed, a simple pressing table, similar in shape to a domestic ironing board, is used. Modern tables have a supply of vacuum to hold the garment in position and dry and set it after ironing. A section of a flat garment part can be held in place while the operator moves the remainder of the part to create a fold or pleat, which they then press. The position of the fold can be marked on the press cover for accuracy. The flat table can be fitted with swivel arms, which present bucks of varied shapes to allow the laying of sleeves, shoulders and collars without distortion or the danger of creasing. Each of these has the vacuum facility. Alternatively, the basic table may consist of a very large flat area, or a smaller curved surface, each with additional sections to be swung into position if required.
The principle is one of flexibility, with some units able to accept a change of pressing surface so that the most suitable shape is always available for the production of a particular batch of garments. A blowing function is also available on some of these pressing surfaces which gives a billowing surface on which to press. This enables some difficult materials, such as thin, hard rainwear fabrics, to be pressed with less risk of seam impressions showing. Self-contained units, incorporating a steam boiler and electrically driven vacuum and air blowing facilities, are used increasingly both in the under pressing of tailored garments and the pressing of unstructured garments, because they can be moved from place to place at much less cost than conventional steam presses or the older irons, both of which are linked to the factory steam supply.
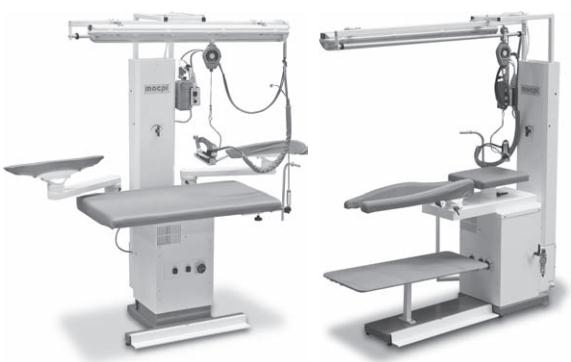
This means that they can be sited within a production line of sewing operations to enable under pressing to be undertaken at minimum cost. Examples of some of the types of ironing unit that are available are shown in Figure 1. The iron is rested at the right-hand end of the flat surface; alternatively the weight of the iron can be taken on the spring fitment on the upper gantry. This reduces operator fatigue in continually picking up and putting down the iron. The use of an iron and pressing table may require considerable skill on the part of the operator, especially when finally pressing complex dresses or blouses, because of the handling involved around a surface shape which is never exactly that of the garment. Additionally, the amount of steam and vacuum used is left to the operator, and the quality of the pressing may suffer if the operator is tempted to hurry in the interests of high output [6].
Steam presses:
A steam press consists of a static buck and a head of complementary shape which closes onto it, thus sandwiching the garment to be pressed. A general-purpose, manually operated press is shown in Figure 2. It consists of a frame carrying the buck, which is generally rounded in shape for pressing a variety of garments, linkages to close the head by a scissors action, a pipe system distributing steam to head and buck, a vacuum system to provide suction through the buck, a table around the buck to aid handling of the garment, and foot controls for head closure and
vacuum, with hand and/or foot controls for steam. These is also a means of varying head pressure. When pressing a garment such as a skirt, a typical pressing cycle might be: apply steam from the buck, lock the head to press the garment, further steam from the head or the buck, release the head, and apply vacuum to cool and dry the garment before it is moved around the buck for the next part of it to be pressed. When pressing is completed, the garment is hung on a hanger. Adequate time of application of vacuum is essential if the garment is not to remain
damp and to distort at this stage. In the case of a manually operated press, the duration of steam, pressure and vacuum are left to the skill and judgment of the operator, as is the manipulation of the garment around the buck, often rather different in shape from the actual garment.
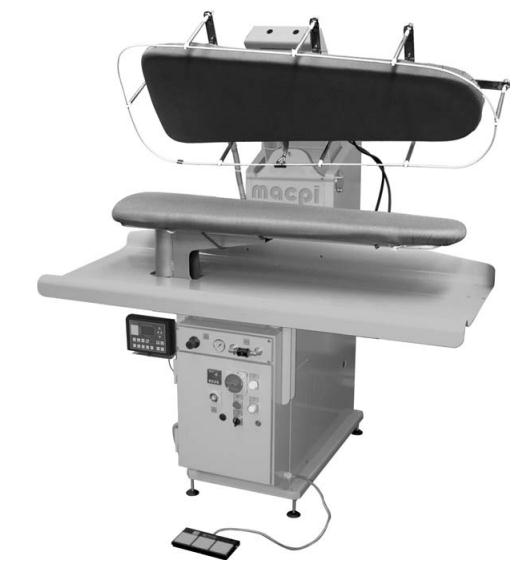
Where large quantities of a garment shape are being manufactured, there is scope for using bucks, and, of course, matching heads, which are close to the shape of the garment. In particular, in men’s jacket production, the total pressing of all the parts of the garment is broken down into many stages, both of under pressing and final pressing, and at each stage a specially shaped press is used. An example of a machine for pressing collars and shoulders is shown in Figure 3. Stocking alternative bucks is a capital intensive practice, and the lead times for supply of new bucks are several weeks long. Consequently, it is increasingly unrealistic to develop garments that require different bucks during pressing. In some cases, an iron is available beside the press for the operator to touch up local areas of the garment before pressing with the head of the press.
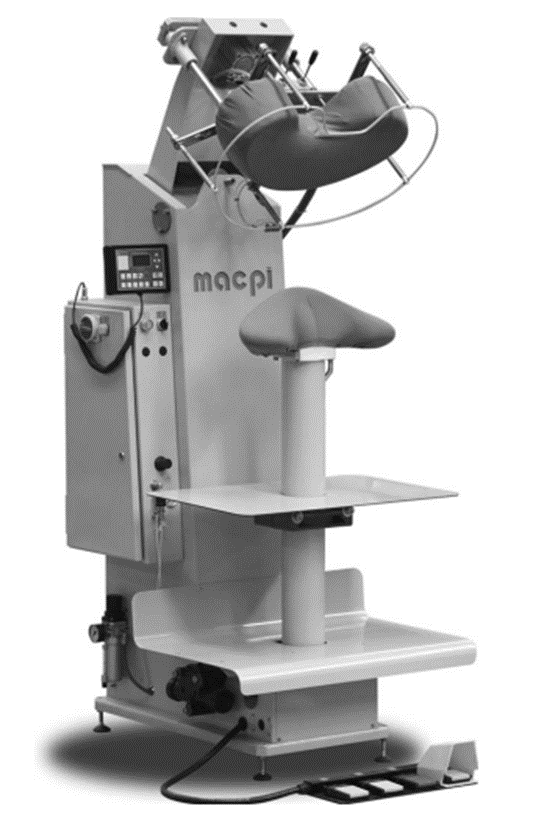
A development in press operation is the carousel press. Here a pair of bucks rotates between the operator and either a single or a double head, depending on whether the bucks are identical or an opposite pair for pressing the left and right of a garment part. The operator loads the garment on to one buck which is then moved away to be aligned under the head, often behind a screen that keeps steam away from the operator. Both scissor-action and vertically acting heads can be used but the latter are increasingly common. While the machine carries out the controlled pressing cycle, the operator loads the other buck. This enables the operator to achieve a much higher output because the handling time of the operation takes place during the pressing cycle, leading to higher machine utilization a four-station carousel press designed to finish trousers without pleats is shown in Figure 4.
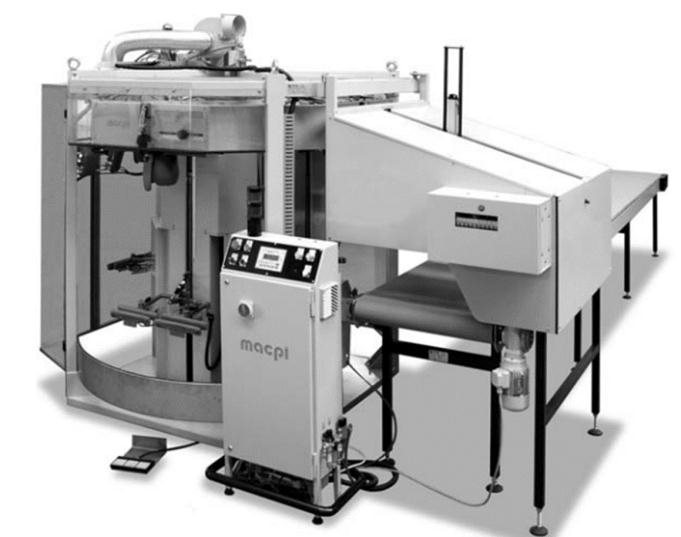
Trouser pressing is conventionally carried out in two operations, in addition to the under pressing of the seam: legging on a flat press, which sets and creases the legs, and topping in a series of lays around the top of the trouser on a contoured press. If the trouser features a pleat at the waistband, the leg crease must be run into it accurately. The problem is to provide firmly set creases at the same time as an even finish to the fabric overall, without impressions of pockets, fly and seams showing. Traditionally, these impressions were removed in a subsequent ‘touching up’ operation with an iron, on those fabrics such as gabardines where the steam press leaves an unacceptable finish, but on most fabrics this should not be necessary. Trouser legging also moulds the legs by pressing away fullness in the underside below the seat area, and by shaping the calves in closer fitting trousers. In addition, the presser must set the crease in the correct position in order that the crease might hang centrally over the shoe of the wearer.
Usually the pattern cutter designs the pattern in such a way that the presser achieves the desired effect by aligning inside leg seam on outside leg seam up to the knee and the inside leg seam then runs back a few centimeters at the crutch. A number of machines combine the topping and legging in one operation by suspending the trousers, from the waistband, vertically over an upright ‘buck’ and pressing from each side.
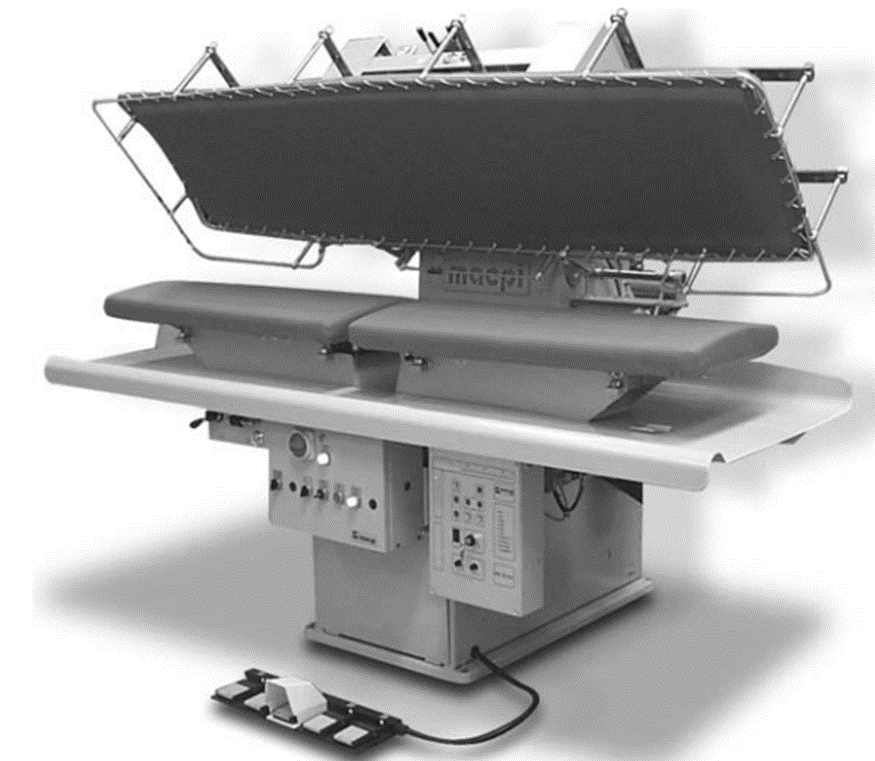
Certain difficulties arise with this method, in particular achieving consistency throughout the size range and flexibility of mechanical pressure on critical areas such as waistbands, pockets and fly. The term ‘trouser’ covers a wide range of garments, including jeans, women’s trousers of perhaps simpler construction and requiring a less sharp crease, men’s trousers including four pockets, and suit trousers. Whether combined topping and legging is acceptable at the moment will depend on the construction of the trousers, the sharpness of the crease and the required quality standards at the point of sale. Thus separate topping is still frequently used. The machinery available for pressing legs also includes double leggers, which press two legs simultaneously, with the top hanging down between two separate bucks, onto which one complete head closes. This is shown in Figure 5. Vertically acting heads, carousels and microprocessor controls are also available. In an attempt to avoid impressions and gloss at the side seam, a split head action (with a vertically acting head) applies steam to the whole leg but no pressure to the seam area. Automatic unloading after pressing, which keeps the legs flat, is also available, the first serious approach to mechanizing the handling elements in a pressing operation. Other than this example, handling between press and hanger is still a significant part of pressing operations [6].
Press cladding:
Bucks of steam presses and the tables used with irons (vacuum boards) are commonly covered with a heat-resistant silicone foam. This is protected on the outside by a top cover of woven polyester (or stretch nylon with the more highly contoured bucks). Although it is generally heat-resistant it is normal to protect the underside of the silicone foam from the continuous heat of the buck by a layer of synthetic felt. The silicone foam has a life of several months without compacting. It remains resilient enough over a long period to absorb the thicknesses of seams and inhibit impressions in the finished garments. Both the stretch nylon and the woven polyester top covers should be smooth enough to allow easy manipulation of the garment from one pressing lay to the next. The heads of steam presses may be covered with a sandwich of materials which contains, from the metal head outwards, a layer of metal gauze, (sometimes copper or more often aluminum) which makes for even distribution of steam, a layer of synthetic felt to protect the next layer, the main layer of knitted cotton padding, and a final
layer of outer cover as on the buck. An alternative for certain fabrics and applications is an aluminum grid plate, with perforations for the emission of steam, and contoured to fi t the head of the press. While these general approaches to covering head and buck are typical, there are many variations according to the needs of the operation. For instance, a need for firmer pressing will reduce the thickness of padding in a few under pressing operations to merely an outer covering [6].
Steam air finisher:
This equipment is often referred to as a steam air bag, a form press or a ‘dolly’ press. It consists of a frame carrying a steam distribution system, compressed air distribution system and a pressing form which is a canvas bag in the approximate shape of the garment to be pressed, i.e. a body shape but with no sleeves. There are controls for steam and air release, and timers controlling the steam and air cycles. The equipment aims to reduce the positioning and repositioning in pressing operations by pressing the whole garment at the same time, though
finishing is a better term in this situation since very little pressure is applied to the garment. The operator pulls the garment on to the form from above, and the form is then expanded to its full size and shape as steam is blown through it from the inside. A cycle of, perhaps, eight seconds’ steaming is followed by a further period of hot air drying, also by blowing from the inside. This equipment can remove accidental creases and refinish the fabric, but will not form creases or mould the garment, and will not help much with cellulosic fabrics. It is extremely useful for garments such as nightdresses, tee shirts and blouses, and is sometimes worth using for simple dresses, even though the hem might have to be pressed flat separately with an iron or a steam press. Distortion along buttoned openings is prevented by a sprung, padded, clamp which holds the section of garment in place and an additional attachment is a spring-loaded sleeve former. Care must be taken when finishing garments in knitted fabrics which may stretch, as the size and shape may be distorted to that of the bag covering the unit. If this is a problem, a slipover may be made from a rigid, woven, press-covering fabric, to the pattern shape of each size of garment, and put on the covering bag as a restrainer before pressing each size of the garment style. An example of a steam-air finisher for shirts, jackets and coats is shown in Figure 6. A variation on the shape described here can be used for jeans and other casual trousers which do not require a crease. The trouser is clamped in a ring at the waist and
clamped again at the ankles. Steam followed by hot air is blown through it, while maintaining slight downward tension on the legs [6].
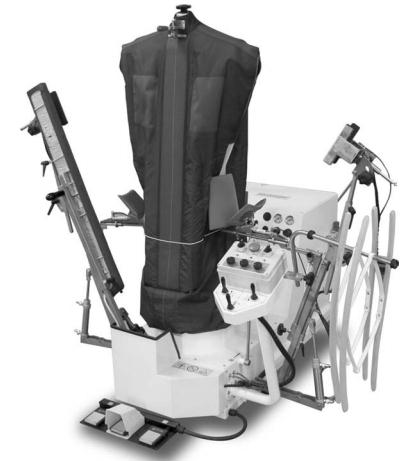
Steam Tunnel:
Another garment finishing process where pressure is not applied to the garments but where handling during the process is reduced is in steam tunnel finishing. It can be used for a variety of simple garments in man-made fibres and blends. In addition to manufacturers, these systems are used extensively by mail-order companies to re- present garments. Some garments on hangers are fed under automatic control through a cabinet on a motorized rail, passed through sections with superheated steam, and dried by air blowing. Alternatively, tee shirts and similar knitwear are loaded on to frames and passed through the tunnel on a conveyor. The tunnel reduces the need for any other pressing process before or after its operation and sometimes eliminates it. The aim of the steam is to relax natural fibres, that of the heat to relax man-made fibres. With the garments on hangers or frames, gravity or tension pulls out the wrinkles, and the turbulence of air blowing provides additional energy to relax wrinkles in woven fabrics. Such turbulence should be restricted with fabrics such as acrylics, since excessive agitation makes the fabric pliable and subject to deformation. This fabric responds well to infrared drying, a feature of some tunnels. The setting of steaming and drying conditions in the tunnel can be varied for different fabrics [6]. The operators have only to load and unload the hangers or frames. An example is shown in Figure 7.
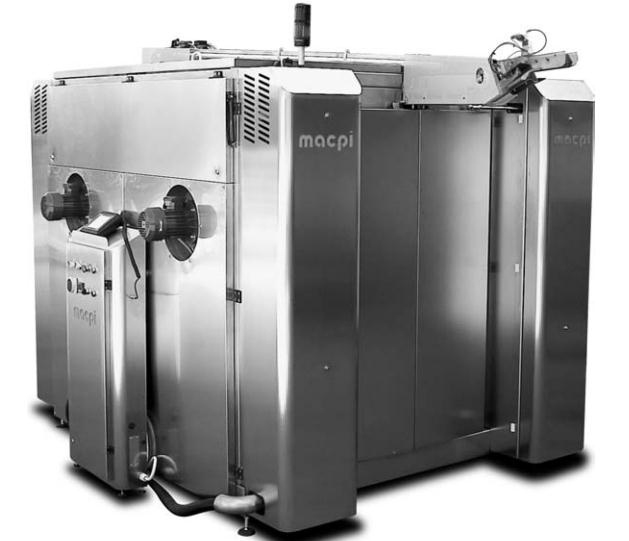
Thread Trimming Machine :
This type of machine can be used on any thread trimming items, such as underwear, shirt, western cloth, western trousers, jeans, t-shirt, hat, embroidery, etc. Especially for clothes with many ends of thread [7]. This machine consists of a suction motor with waste collector and its blade is plated with titanium [8]. An example of thread trimming machine is shown in figure 8.
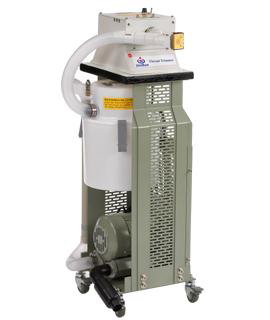
Thread Sucking Machine:
Thread sucking machine is extensively used to remove dust particles and all loose thread from finished garments and textile products through a specially designed suction operation simultaneously creating an oscillation, similar to dusting of garments. It contains easily removable lint filter that capable for collection of all lint, loose thread and dust particles [9]. An example of Thread Sucking Machine is shown in Figure 9.
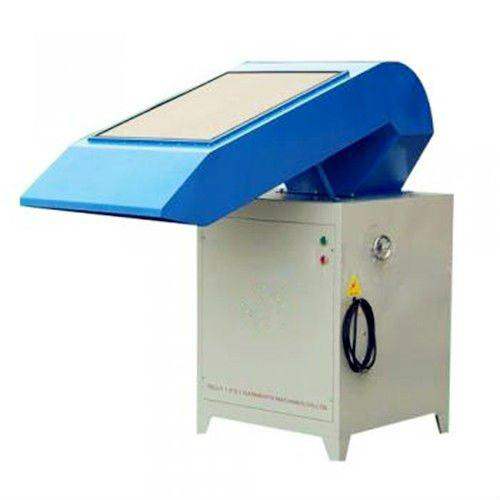
Stain Removing Machines:
Stain removing machine removes practically all stains by shooting compressed air and chemical at the stain. A hot air and steam gun enables removing of tough to remove stains [10]. An example of stain removing machines is shown in figure 10.
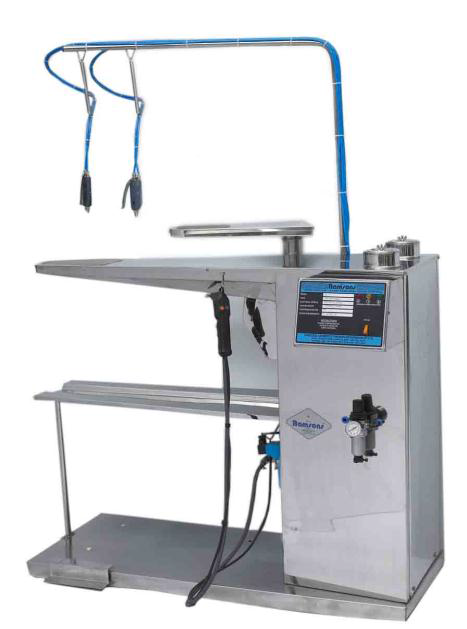
Automatic Conveyor & Stacking Systems:
Automatic conveyors are the fast, efficient way to transport garments without the use of expensive and inconsistent labor. Automatic shirt stackers reduce labor costs and increase accuracy by automatically stacking and counting T-shirts and other garments. IC-120 shirt conveyor is designed to accept materials fed directly from bag loading & sealing systems and from other packaging machines. It stacks T-shirts and similar garments based on user-set counts [11]. An example of Automatic Conveyor & Stacking Systems is shown in Figure 11.
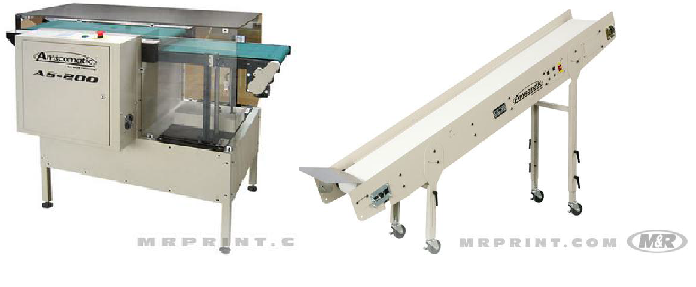
Automatic Folding Machine:
Automatic Folding machine is designed to fold precisely a wide variety of garments and other textile items. A significant technological breakthrough bottom pulling dual-belt (upper and lower) transport system makes it possible to fold garments. Folding plates electronically adjust to the desired width while staying parallel to each other. This allows tighter, more consistent folding on all types of products. The entire garment transport system uses a timing belt drive, which runs quieter [11]. An example of Automatic Folding Machine is shown in Figure 12.
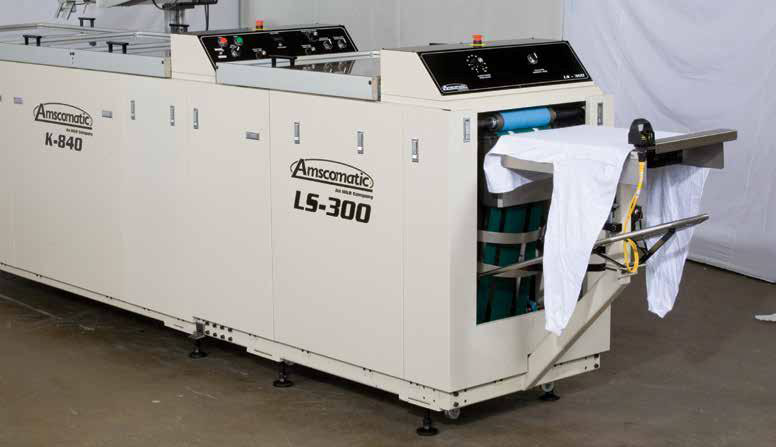
Automatic Bagging and Sealing Machine:
Automatic Garment Bagging Systems simplify bagging & sealing of many products. Bagged garments stay clean and folded, and tags & labels stay attached. It handles wicketed bags of various widths and lengths. It features a convenient blower to open the bag and a pneumatic compression plate that gently squeezes the bagged product to eliminate excess air and give the product an attractive appearance. The heating element creates an airtight seal [11]. An example of Automatic Bagging and Sealing Machine is shown in Figure 13.
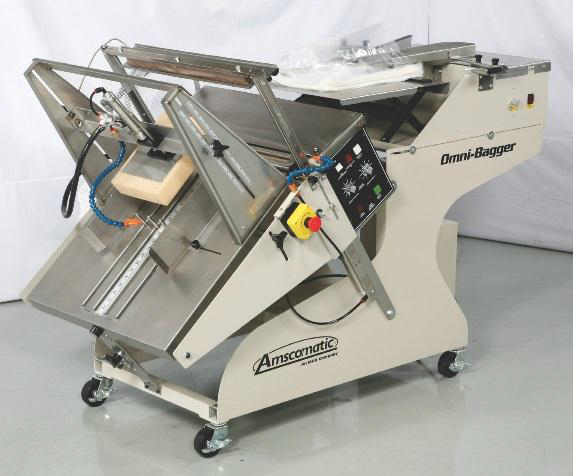
Automatic Card Insertion Machine:
Automatic Card Insertion Systems for Garments replace the standard drape table and integrate
with automatic folding machines, inserting a wide variety of cards and stiffeners into T-shirts
and other garments during the folding process. These exceptionally fast card feeders keep pace
with the highest folder cycle speeds. They insert a wide variety of non-curled cardboard and
chipboard stiffeners, and the card magazine can be refilled quickly to help maintain high
productivity levels [11]. An example of Automatic Card Insertion Machine is shown in Figure
14.
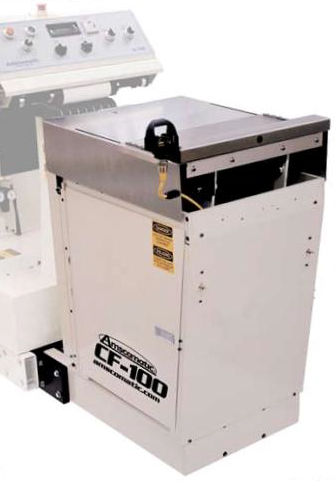
Automatic Garment Label & Tag Application Systems:
Automatic Garment Label & Tag Application Systems improve consistency and reduce labor costs by bringing automation to label attachment and T-shirt tagging. The high-speed label applicator automatically applies labels to garments as they pass through an automatic folding machine. Semi-automatic garment taggers let users apply up to three tags to T-shirts, caps, sweats, towels, and other fabrics [11]. An example Automatic Garment Label & Tag Application Machine of is shown in Figure 15.
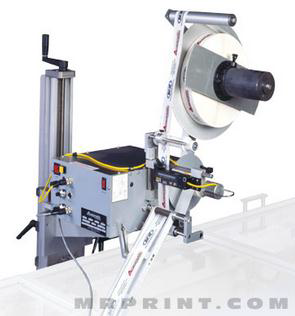
Automatic Metal Detector Machine:
A metal detector is an electronic instrument which detects the presence of metal nearby. Metal detectors are useful for finding metal inclusions hidden within garments or clothing [12]. Needle detector is widely used in apparel industry for identifying needles and staples. It has the capability of automatic balance and also has a strong sensitivity for ferrous metals. It is one of the most important inspection equipment in the quality of sewn products [13]. The simplest form of a metal detector consists of an oscillator producing an alternating current that passes through a coil producing an alternating magnetic field. If a piece of electrically conductive metal is close to the coil, eddy currents will be induced in the metal, and this produces a magnetic field of its own. If another coil is used to measure the magnetic field (acting as a magnetometer), the change in the magnetic field due to the metallic object can be detected [12]. Automatic Metal Detector Machine is shown in figure 16.
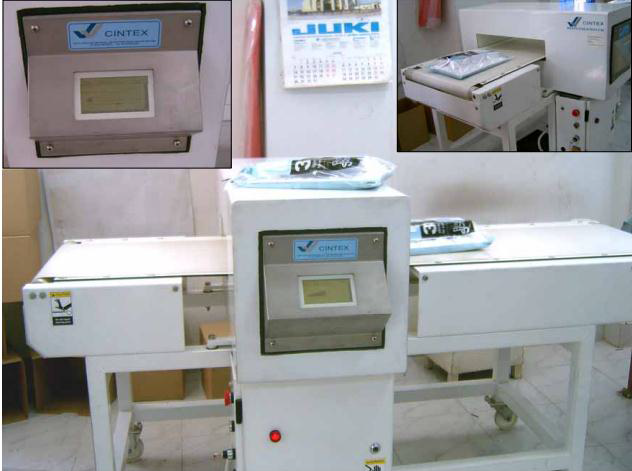
Apparel finishing machineries play an important role to produce a garment perfectly. Advanced machineries discussed above increase production rate as well as reduce the demand of labor though initial buying cost is high than conventional one. Every garments factory should have these machineries for fast, cleaner and efficient production.
References :
1. Prasanta Sarkar, Garment Manufacturing Process Flow Chart, Retrieved from http://www.onlineclothingstudy.com/
2. Kashem, M. A. (2006). Garments and Technology. Gronthonir prokashoni, Dhaka, pp- 296
3. Cooklin, G., Hayes, S. G., McLoughlin, J., & Fairclough, D. (2011). Cooklin’s Garment Technology For Fashion Designers. John Wiley & Sons.
4. Marsh, J.T.; An Introduction to Textile Finishing, Chapman & Hall Ltd, London, 1947.
5. Anon.; Pressing without pressure’, Afr. Text., February/March, 1990, p. 50.
6. Tyler, D.J. (Ed.); Carr & Latham’s Technology of Clothing Manufacture, Blackwell
Publishing, Oxford 2000
7. http://www.b2bchinasources.com/showroom.php?c=3590&f=5&p=0000042053
8. http://www.focus-gmt-tech.com/product/us-100ez
9. http://www.sunrisetechnicalservices.net/thread-sucking-machine-166957.html
10. http://www.ramsonsindia.com
11. http://www.mrprint.com/
12. Metal detector. (2015, January 20). In Wikipedia, The Free Encyclopedia. Retrieved 07:16, April 5, 2015, from http://en.wikipedia.org/w/index.php?title=Metal_detector&oldid=643373580
13. http://www.smmsengineering.com/textile-metal-detector.html