What is Quality?
Each & every product features some special characteristics for which it is in demand by consumers. History of quality is as old as human civilization itself. Aristotle 2500 years ago defined quality as following:
1. Quality is the difference between products.
2. It is the goodness or badness in a product.
This definition holds true till this date. However, in general terms, quality encompasses important characteristics of a product for which, it is in demand. Quality is also referred to as “conformance of goods to buyers’ specifications”. ISO 9000: 2000 defines quality as “degree to which a set of inherent characteristics fulfill requirements”.
On what Quality depends on?
Quality depends on two things. Such as given below:
Form: It represents features of a product in terms of shape, size, style, design & measurements.
Content: It represents features expressing internal quality, implying quality of raw materials & the value additions attached to it.
Why quality is important?
- Every product must feature functional characteristics as well as some other aspects related to its shape, size & design. Consumers always demand following expectations of the purchased product:
- The product must satisfy the consumer in terms of beauty, attractiveness, taste, shape, design & longevity etc. depending on the type of product.
- A product devoid of quality has no demand among consumers & as such, has no salability. Excellent quality characteristics enhances salability of the goods & are the keys to profitability for the manufacturer or the seller.
- Most importantly, some criteria of customer satisfaction are negotiable but quality is such a factor that it is not at all burgeoning.
What are the Types of Quality?
As per excellence of satisfaction, quality may be grouped into three categories:
- Quality of general acceptance;
- Quality of satisfaction;
- Quality category of higher delight.
A black & white television now-a-days brings in only quality of general acceptance while a color television provides to the buyer quality of satisfaction. On the other hand color television with a remote control brings forth quality of great delight to buyer.
What are the Quality characteristics in apparel?
In a clothing factory, manufactured garments must possess specified quality characteristics.
They are given below:
- Measurements specified by the buyers;
- Specified sewing & stitching quality
- Raw materials must possess specified quality
- Garments must possess specified design characteristics.
- Assortment specified by the buyer
- Finishing, packing, packaging must be specified by the customers.
So, quality of garments implies whether the specified garment has been produced with specified raw materials, with buyer specified stitching & sewing quality, with specified sizes, shapes, design & assortment.
In clothing industry, demanded quality characteristics of the garments are informed to the manufacturer through work sheet, approved sample & size spec etc.
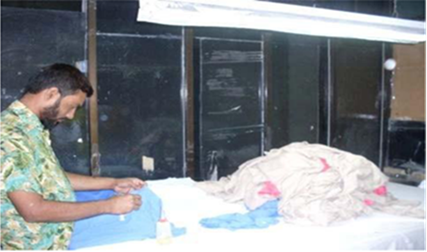
What is Quality Control in Apparel Industry?
Quality control is the operational techniques and activities that are used to fulfill requirements for quality. On the other words, a system applied to manufacturing operations to monitor & regulate production process continually so that products meet specification.
To control the quality of garments or products two techniques are followed, such as :
- Testing and
- Inspection
Testing:
To those engaged in the production, distribution and consumption of textiles, testing can be a valuable aid provided tests are made the results must be studied carefully so that the right course of action may be taken. Testing instruments cannot make decisions and in the end some person has to interpret the data and issue the necessary instructions for future action.
Inspection:
The inspections are done to control the quality is means by examining the products without any instrument. To examine the fabric, sewing, button, thread, zipper, garments measurement and so on according to specification or desired standard is called inspection. There are so many facilities for inspection in every section of garments industries. The aim of inspections is to reduce the time and cost by identifying the faults or defects in every step of garments making.
What is Quality Assurance?
To carry out all those planned and systematic actions necessary to provide adequate confidence that a product or service will satisfy given requirements for quality is called Quality assurance. On the words, this is a system to assure that product & services meet customer requirements.
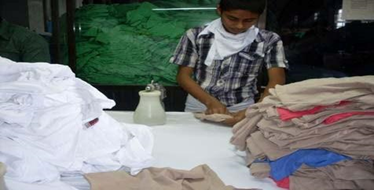
What is Quality Management System?
Quality Management System (QMS) is a set of interrelated techniques, measures and management system designed to prevent defects from occurring or if they occur at all. Countermeasures are adopted immediately so that they do not recur. QMS takes recourse to preventive as well as remedial measures.
What is Quality Management System in the garments industry?
A number of systems, measures & techniques are used so that only quality goods are produced in the first place and defects do not originate at all. If they occur at all, there must be corrective action so that they are eliminated in the preliminary stage and would not reappear. QMS generally employs the following measures, techniques that ensure that only quality good are produced:
* Inspect all incoming, in-process & final goods to ensure quality of goods
* Ensure that all patterns & grading of patterns are okay.
* Inspect marker and check if it is okay and within consumption.
* Inspect spreading, cutting & numbering.
* Ensure if relaxation time was given to knit fabric.
* Install in-line inspector in the sewing lines.
* Install Traffic Light Chart system or other system to monitor quality in production line.
* Inspect 100% goods delivered from sewing lines.
* Inspect the table quality passed garments with Statistical Technique.
* Control reject goods so that they do not mix-up with quality passed goods.
* Control repairable goods, washable goods so that they can be double checked to ensure quality.
* Inspect goods with right equipment’s and in right conditions.
* Inspect ironing, folding.
* Make repeat inspection of garments prior to poly-bagging.
* Inspect poly-bagging & assortment.
* Final table inspection in conducted prior to shipment of goods.
* Impart training QA personnel so that they can easily identify defects & understand the causes of defects.
* Impart training QA personnel on Statistical Methods.
* Make continuous improvement plans & implement them.
What is Total quality management?
This is one of the latest concepts of management that can ensure the highest standard of quality and productivity ensuring good for all of the workers, management and society. In this system, quality of management and actions are ensured by assuring quality at all stages from vision, planning, purchase, store, cutting, sewing, inspection, packing, administration, welfare, personnel motivation etc. TQM envisages high work standard, work-environment, managerial standard, motivation etc. Thus comes the concept of production system with minimal or “zero de-fact”.
What is the Job description of Quality Manager?
The quality manager is a very important official in a garment factory. Customer satisfaction, reputation of the company, to a large extent, depends upon him. His job description is given below:
1. He will install or maintain a right Quality Management System to ensure quality of product;
2. He will ensure that the QMS is in place & working as envisaged;
3. He will ensure that the existing QMS satisfies the buyer;
4. He will look for ways of improving existing QMS so as to exceed expectations of the customer;
5. He will ensure that buyer’s specifications are properly understood;
6. If there is any ambiguity/ confusion, he will confirm buyer’s actual Specifications;
7. He will ensure that AQL of the company is properly maintained & exceeded.
8. He will ensure that all incoming, in-process & final goods are properly inspected & documented.
9. He will ensure that all goods coming in the store are rigorously inspected for quality & quantity;
10. He will ensure that Traffic Light Chart system of in-line inspection system is installed & working;
11. He will install both preventive & remedial measures against occurrence of any defect;
12. He is responsible for failure of quality passed garment;
13. He will ensure that all of his personnel are trained on their topics;
14. He will ensure continuous training of personal to enhance their skill;
15. He will ensure rigorous control of rejects;
16. He will ensure rigorous control of repairable & washable garments;
17. He will plan for year-wise improvement of quality;
18. He will prepare a quality manual for the company so that company’s quality policy & procedures are known to all and implemented at all levels;
19. He will ensure that quality manual includes all policy, procedures, methods & measures so as to unify actions;
20. He will monitor performance of suppliers of raw-materials;
21. He will have his personnel motivated.
22. He will ensure that supplier-customer chain in maintained in the production process;
23. He will ensure that production commences only when worksheet approved sample & swatch card are at hand.
ISO: According to ISO,
Quality is the fulfillment of specified requirements of the product or service’ another definition of ISO,
The totality of features & characteristics of product or service that bear on its ability to satisfy stated or implied needs. The term usually combined with a number or name used to identify textile products. A relative term used to indicate the perceived merits of similar products for same end use.
• Quality varies from customer to customer.
• Quality is the reflection of customers.
Organogram of Quality Management System in the garment Industry:
Quality Management System:
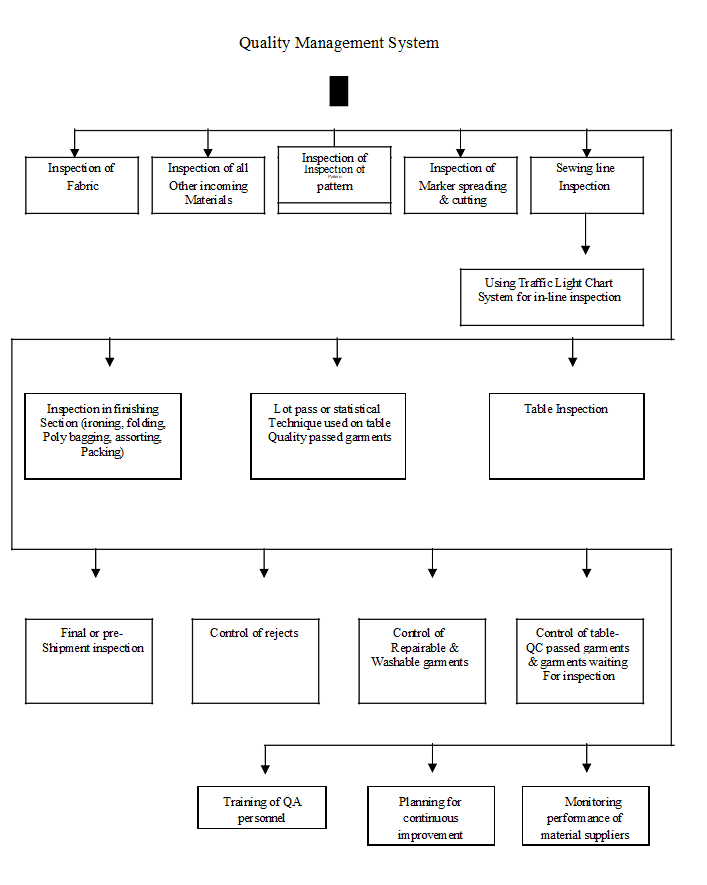
Organogram of Quality Team :
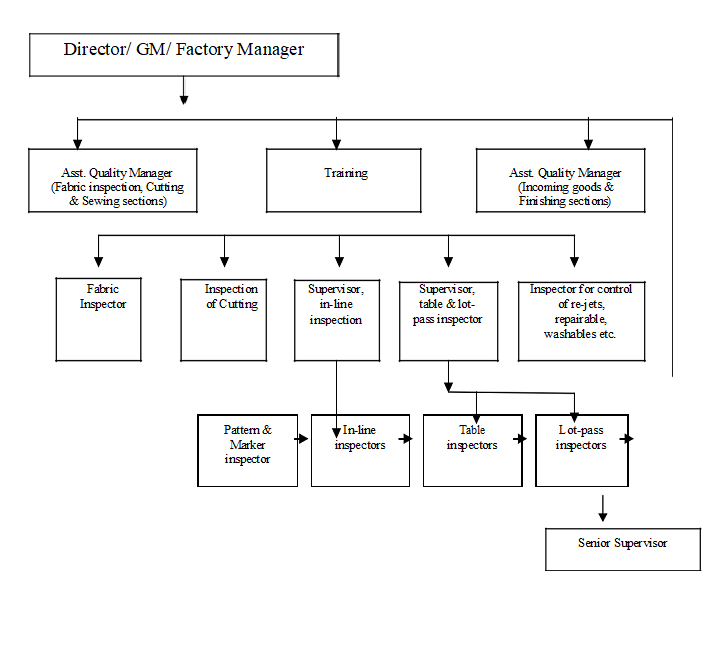
References :
- Bangladesh Garment Manufacturers and Exporters Association, “RMG Industry: Trade Information”, 2018.
- ISO 9001:2008
- www.textileflowchart.com
- www.indiantextilejournal.com