Inspection:
The inspections are done to control the quality is means by examining the products without any instrument. To examine the fabric, sewing, button, thread, zipper, garments measurement and so on according to specification or desired standard is called inspection. There are so many facilities for inspection in every section of garments industries. The aim of inspections is to reduce the time and cost by identifying the faults or defects in every step of garments making.
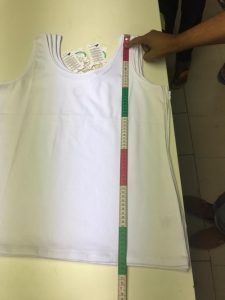
To do success in inspection, the process can be run by maintaining following “inspection loop”.
- Inspection
- Identify the defects or faults
- Knock the appropriate person
- Identify the reasons of defects or faults
- Remove the defects or faults.
Mainly inspections are done in three steps in garments industries. The steps are:
- Raw material inspection
- In process inspection
- Final inspection.
For inspection to be effective the entire inspection loop as shown in below figure must be completed.
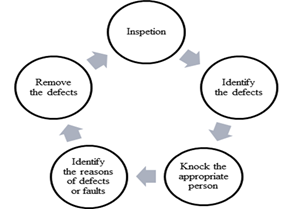
Trimmings and Accessories Inspection:
Trimmings and accessories inspection is a critical matter in the apparel manufacturing industry. To achieve the desired quality apparel or clothing, proper trimmings and accessories inspection processes have to follow. It should be noted here that, the total process of trims and accessories inspection should be done by an experienced quality inspector. This article has presented the proper method of trims and accessories inspection with the inspection defect checklist for clothing accessories and trimmings.
FABRIC INSPECTION:
- Fabric Inspection is systematic observation of fabrics to decide whether it meets: Client’s specification in terms of count/construction, color, design, measurement specifications, hand/feel and other specific quality parameters laid down by the clients.
- This will minimize the quantity of panels or garments rejected for fabric faults, thereby ensuring the quality of the finished goods. Fabric inspection is also considered as pre-production inspection for garments or other textile products.
BENEFITS:
- The main objective of the inspection is the detection of defects and non-conformance as early as possible in the manufacturing process.
- Minimizing the time and money wastage by correcting the defective raw materials.
- Fabrics supplied to customers meet their specifications and standards; thereby they face less customer returns and recalls.
- Fabric inspection ensures to minimize the rejection of cut panels or rejected garments due to fabric faults.
- Cutting inspected and approved fabric ensures not only finished garment quality but also reduces rejects, improves efficiency and timely deliveries.
FABRIC INSPECTION SYSTEM:
There are various fabric inspection systems. Some commonly used Inspection systems are
- 4- Point system.
- 10-Point System.
4-POINT SYSTEM:
The 4-Point System, also called the American Apparel Manufacturers (AAMA) point-grading system for determining fabric quality, is widely used by producers of apparel fabrics.
The 4-Point System assigns 1, 2, 3 and 4 penalty points according to the size and significance of the defect. No more than 4 penalty points can be assigned for any single defect. Defect can be in either length or width direction, the system remains the same. Only major defects are considered. No penalty points are assigned to minor defects.
In this system, one should inspect at least 10 percent of the total rolls in the shipment and make sure to select at least one roll of each color way.
Fabric defects are assigned points based on the following:
Table-1: Defects length for warp :
Defects length for warp and way and weft way | Points |
Up to 3” | 1 |
3”~6” | 2 |
6”~9” | 3 |
Above 9” | 4 |
Table-2: Defects area for holes and openings:
Defects area for holes and openings | Points |
1” or less that 1” | 2 |
Above 1” | 4 |
Note: It must be remembered that, defected point must not be more than 4 in each yard.
For example: for 100 square. Yds. Inspection ..
Table-3: 4-point system :
Defects length | No of faults | No of points | |
Up to 3” | 10 | 10X1=10 | |
3”~6” | 5 | 5 X 2 | = 10 |
6”~9” | 2 | 2 X 3 | = 6 |
Above 9” | 0 | 0 X 4 | = 4 |
Total = 26 | |||
Calculation of total points per yards :
In 4 point system fabric quality is evaluated by unit points/100 sq. yds.
Points / 100 sq. yd. = (Total points in roll * 36 * 100)/ (Fabric length in yards * Fabric width in inches)
normally fabric roll containing 40 points per 100 square yard are acceptable.
Example: A fabric roll 120 yards long and 46 inch wide contains following defects.
Table-4: Calculation of total points per yards
4 defects up to 3 inch length
3 defects from 3 to 6 inch length 2 defects from 6 to 9 inch length 1 defect over 9 inch length 1 hole over 1 inch |
4 x 1
3 X 2 2 X 3 1 X 4 1 X 4 |
4 points
6 points 6 points 4 points 4 points |
Total defect points | 24 Points | |
Therefore,
Points/ 100 sq. yards |
= (24 X 3600)/(120 X 46)
= 15.652 points |
AQL (Acceptable Quality Level):
The AQL is the maximum percent defective that for the purpose of sampling inspection can be considered satisfactory as a process average. When a customer designates some specific value of AQL for a certain defect or group of defects he indicates to the supplier that his (the customer’s) acceptance sampling plan will accept the great majority of the lots or batches that the supplier submits, provided the process average level of percent defective in these lots or batches is no greater that the designated value of AQL. Thus, the AQL is a designated value of per cent defective that the customer indicates will be accepted most of the time by the acceptance sampling procedures to be used.
The AQL is generally expressed in per cent (%). The AQLs most widely used in apparel industry are 2.5, 4.0, 6.5, and 10.0 depending on the price and item. For example, for low price items and children’s wear AQLs of 6.5 and 10.0 may be quite appropriate, however, for higher price items AQLs of 2.5 and 4.0 may be appropriate.
Sewing Thread Inspection in Apparel Industry:
During sewing, the garments, sewing thread drawn-off hamper deeply to the garments production and quality of garments. Normally, sewing threads in the needle move at a speed from 140-160km per hour during the running of sewing machines. It can reduce the strength of sewing thread 2 to 32% due to the friction between the threads and different parts of the sewing machine. For this reason, sewing thread inspection is very important before buying the sewing thread from the market. As its importance in the readymade garments industry, this article has shown some key inspection matters which ensure the right quality of the thread.
Sewing Thread Inspection in Garments Industry:
Sewing threads are bought by checking for having the following properties:
(a). Thread construction or ticket number,
(b). Sew-ability of sewing thread.
Both the key inspection matters have explained the below:
Thread construction or ticket number:
In the apparel manufacturing industry, the ticket number is a commercial numbering system. Normally, the ticket number is the manufacturer’s reference number for the size of a given thread. In fact, the size or count of sewing thread is called a ticket number. The following are the tests done to identify thread construction or ticket number.
- Thread count,
- Thread elongation,
- Thread balance,
- Number of twists,
- Thread tenacity,
- Thread ply.
Sew-ability of sewing thread:
The ability of sewing a thread is called sew-ability. To identify the sew-ability, 3 thread packages are collected from a lot and sewn 100 yards length, and here also noted the running performance of the sewing machine. It is done to determine the ability of sewing thread compared with the fault-free thread. Also, the following properties are inspected to determine the sew-ability of the thread:
- Imperfections of thread,
- Finishing of thread,
- Thread Package density,
- Color of thread.
- Yardage of thread,
- The winding of thread.
Sew ability:
The sewing fitness of a thread is called its sewability. In order to determine the sewability, 3 packages of thread are taken from a lot, 100 yards of sewing is done and the running performance of the machine is listed. The main objective of this test is to know the capacity of flawless and beautiful sewing of each thread in a normal condition and at the highest speed of the sewing machine. During the test of sewability, the other properties of thread that should be examined are as follows:
- Imperfections: If there is any knot or slub in the thread, the thread will break frequently, causing decreasing of both the efficiency and production of the machine and the quality of the produced goods will also be deteriorated.
- Finish: The finish of thread is mainly meant to lubricant that helps thread to pass through needle eye and the various guides of machine. The amount of lubricant in threads may be from 3 to 15%. The amount of lubricant should be in the same percentage for each package of thread in a lot otherwise various problems will arise sewing.
- The color of thread: Any color of thread including white, must match with its sample and the color of the thread in the same lot should not differ considerably. Otherwise, adverse effect may result on the quality of the garments.
- The package density: Should not have any difference in density of a package or a cone from another cone. If there is difference in density, the efficiency and productivity of the machine will decrease due to frequent adjustment of the tension of the thread.
- Winding: Thread should be properly wound in the package. Otherwise thread can break frequently during sewing due to the snarling of thread after coming out of the package. As a result, both the production and the quality of goods may be damaged.
- Yardage: The length of thread in a package of thread has to be within 2% of the mentioned length (yardage) otherwise that package may be cancelled.
Zipper Inspection:
Chain or zipper is a special part of a garment, which if defective, the garment may be unfit for wearing. Need to be ensured beforehand about the below issues so that the defects related to the zippers should not arise.
- Dimension: Need to be ensured beforehand about the measurement of the length of the chain and the width of the tape so that it does not create any problem for shortage of dimension during attaching to the garments.
- Stops: The stops ends at the upper end and the lower end of the chain must be stopped by sewing in garments properly, fairly and in well secured.
- Uniform color: The color of the chain tape must be uniform.
- Puckering: Need to be ensured so that no puckering in garments happen after attaching of the chain by sewing.
- Dimension and color: After washing or dry cleaning or ironing, the dimension of the chain or its color should not be changed.
- Slider: The movement of the slider through the chain should be easy but care should be taken so that the slider can be well locked in the chain.
- Arrow mark: The chain should be attached in the garment as per the arrow mark in the slider.
Button Inspection:
- Button holes should be large, clean, and free from flash, so that it will not cut the thread.
- Button holes should be located properly.
- Button thickness should be uniform.
- Button shade should be within tolerance.
- Button should be able to withstand laundering, dry cleaning, and pressing without any change or deform
- Button size should be as specified.
- In case of any special requirements button should have all.
Ref.: