Linen is a long fibre made from the fibers of the flax plant. Linen is very strong and absorbent and dries faster than cotton. Because of these properties, linen is comfortable to wear in hot weather and is valued for use in garments. It also has other distinctive characteristics, notably its tendency to wrinkle. Many other products, including home furnishing items, are also often made from linen.
- Linen is a cellulosic fibres derived from the stem of the flax plant or linum usitatissimum which is one of the oldest cultivated plant In human history.
- Fragments of straw, seeds, fibres, yarns, and various types of fabrics dating to about 8000 BC have been found in Swiss lake dwellings.
- Flax is an annual plant, which means it only lives for one growing season.
- From seed-planting, it is ready to be harvested in about a hundred days. Unless the weather is particularly warm and dry, flax requires little watering or attention during this time.
- It grows to about three or four feet tall, with glossy bluish-green
- Flax is grown in many parts of the world, but top quality flax is primarily grown in Western European countries and Ukraine.
- In very recent years bulk linen production has moved to Eastern linen market in India is spread over southern most part. Kochileaves and pale blue flowers–though on rare occasions, the flowers bloom red. Europe and China. is the centre of the production of Linen.
- Composition of linen is as follows :-Cellulose : 92%Hemi Cellulose : 2%Lignin: 4%: & Others 2%
Cellulose is the principle element of Linen:
Structure of Hemi Cellulose:
Morphology of Linen:
Cross section of Linen:
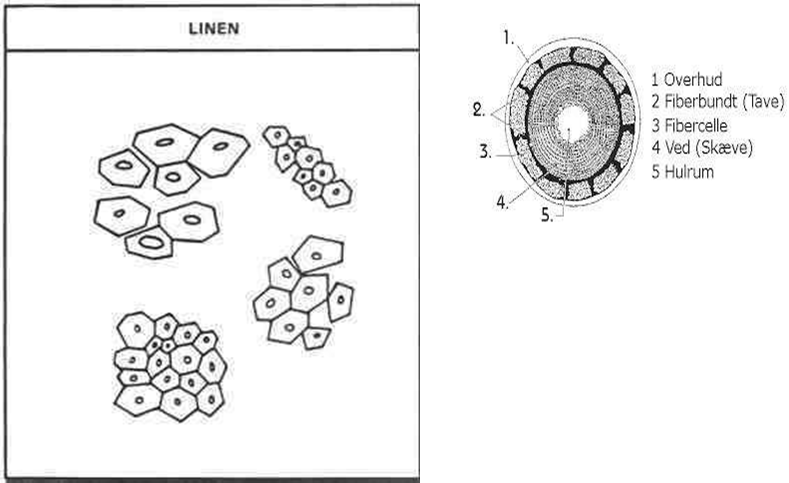
Physical Properties of Linen:
- Specific Gravity: Specific gravity of linen fibre is 1.50.
- Moisture Regain (MR %): Standard moisture regain is 10 to 12%.
- Resiliency: Very poor.
- Effect of Heat: Linen has an excellent resistance to degradation by heat. It is less affected than cotton fibre by the heat.
- Effect of Sun Light: Linen fibre is not affected by the sun light as others fibre. It has enough ability to protect sun light.
Chemical Properties of Linen :
- Effect of Acids: Linen fibre is damaged by highly densified acids but low dense acids does not affect if it is wash instantly after application of acids.
- Effects of Alkalis: Linen has an excellent resistance to alkalis. It does not affected by the strong alkalis.
- Effects of Bleaching Agents: Cool chlorine and hypo-chlorine bleaching agent does not affect the linen fibre properties.
- Effect of Organic Solvent: Linen fibre has high resistance to normal organic solvents.
- Dyes: It is not suitable to dye. But it can be dye by direct and vat dyes.
- Effect of Micro Organism: Linen fibre is attacked by fungi and bacteria. Mildews will feed on linen fabric, rotting and weakling the materials. Mildews and bacteria will flourish on linen under hot and humid condition. They canbe protected by impregnation with certain types of chemicals. Copper Nephthenate is one of the chemical.
- Effects of Insects: Linen fibre does not attacked by moth-grubs or beetles.
Manufacturing process of Linen fabrics :
The manufacturing process flow chart is as below…
Harvesting Flax Fibre
↓
Retting
↓
Scutching
↓
Spinning
↓
Weaving
Separating the Flax Fibre:
- The xylem and phloem of plants are bundled together by calcium ions and a sticky protein called pectin, which must be broken down in order to separate the valuable bast fibres from the plant’s vasculature so that they can be processed and spun into yarn.
- This is achieved via a process called Retting.
Retting:
- Water retting is the most widely-employed practice and produces the highest quality fibres.
- It is best accomplished in stagnant or slowly-moving waters, like ponds, bogs and streams. As a rule, the more stagnant the water source, the more abundant the bacterial fauna and the faster the retting process.
- The bundles are steeped in water at least 60 cm to 100 cm depth. The retting process is completed in 8 to 30 days, days, when the barks separate out easily from the stick or wood and the fibres are ready for extraction.
- Dew retting is the preferred method in areas where water sources are limited but that enjoy warm daytime temperatures and heavy night time dews.
- Flax stalks are spread out evenly in a grassy field, where the combination of air, sun, and dew causes fermentation which dissolves much of the stem within 2-3 weeks.
- Flax can also be retted chemically, which speeds up the process. It is, however, more harmful to both the environment and the fibres themselves, and is therefore not preferred.
Scutching:
- Dressing of Flax is carried out by the process called Scutching.
- Scutching involves scraping a small wooden knife down the length of the fibres as they hang vertically, pulling the broken woody bits away from the fibre.
- The separated bast fibres are next heckled, or combed through a bed of nails that splits and polishes the fibres, and removes the shorter tow fibres from the mix.
- These tow fibres can then be spun into a coarse yarn from which low-quality linen products are made.
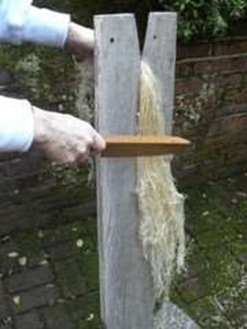
Spinning:
- The separated flax fibres, called stricks, are traditionally spun by hand using a Distaff.
- A distaff is simply a long vertical pole that attaches to a spinning wheel from which the fibres are hung. This helps keep the fibres organized and prevents them from turning into a tangled mess.
- Spinning involves twisting together the drawn out strands of fibre to form yarns, then winding the yarn onto a Bobbin, or spool.
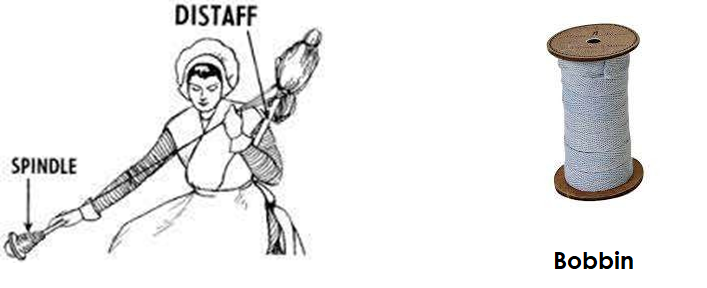
Then weaving and knitting is done to make the fabrics.
Applications of Linen:
- Apparel – suits, dresses, skirts, shirts etc.
- Home and commercial furnishing items – table cloths, dish towels, bed sheets, wallpaper / wall coverings, window treatments etc.
- Industrial products – luggage, canvas etc.
- Used as blend with cotton
Ref.: