Though 2D weaving is widely used on a vertical surface, it is a little outdated for industrial 3D fabric. That’s why, with regular development, 3D weaving has been introduced. It is efficient in creating proper and clear 3-dimensional orthogonal surfaces.
What is 3D fabric weaving?
3D weaving is a modification of conventional fabrication mechanisms. In this method, weft, warp, and binder fibers run across, along, and through the fabrics in the X, Y, and Z directions, respectively. More specifically, in 3D fabric, thickness is a major concern. Apart from normal fabric, it shows more thickness in the Z direction. As in 3D weaving, layers of warp and weft yarns are used, and up to 10cm of thickness can be formed.
Classification Classification:
We can classify 3D-woven fabrics according to the binder path of the multilayer and the interlacement angle between the binding yarns and the weft yarns.
- When the interlacement angle is 90º, the structure is referred to as orthogonal.
- If it is not, it is called an angle interlock.
Those two categories can be further divided into two classes.
- Through-thickness: When the binder goes all the way from top to bottom of the fabric.
- Multilayer: when the binding yarns only bind internal layers of the fabric together.
Process of 3D Fabric weaving:
3D weaving is regularly updated with modern mechanisms, as it is needed to work on complex surface geometrics. But there is a basic story to every procedure.
- At first, multiple sets of warp & weft yarns are prepared. These yarns can be made from various materials, such as fibers, filaments, or even metal wires, depending on the desired properties of the final 3D textile structure.
- In 3D weaving, shedding doesn’t only indicate the raising & lowering of selected warp yarns. It allows the manipulation of multiple layers of warp yarn in three dimensions.
- After creating the shed, the weft yarns are entered using specialized insertion mechanisms. The basic criteria that justify the name happened here. Contrasting conventional weaving, in 3D weaving, the weft yarns are also inserted in the thickness direction, adding dimension to the fabric structure.
- After the shape is created, they are condensed or beaten up against the previously woven layers. It ensures tight interlacement and cohesion in the fabric structure.
The above processes are repeated a certain number of times until the desired layers are achieved. Ultimately, it creates a fully integrated, three-dimensional textile structure.
Application:
3D weaving is more popular in technical textiles. It covers the area of advanced composites. Other than that, it has wandered into airplane bodies, medical textiles, packaging, sports goods, high-performance powerboats, etc. Especially in medicine, the basic application is in the weaving of vascular prostheses. Vascular prostheses are used to replace defective blood vessels in patients to improve blood circulation.
Besides, this process is used to reduce material cost & handling time as well as deliver better mechanical properties.
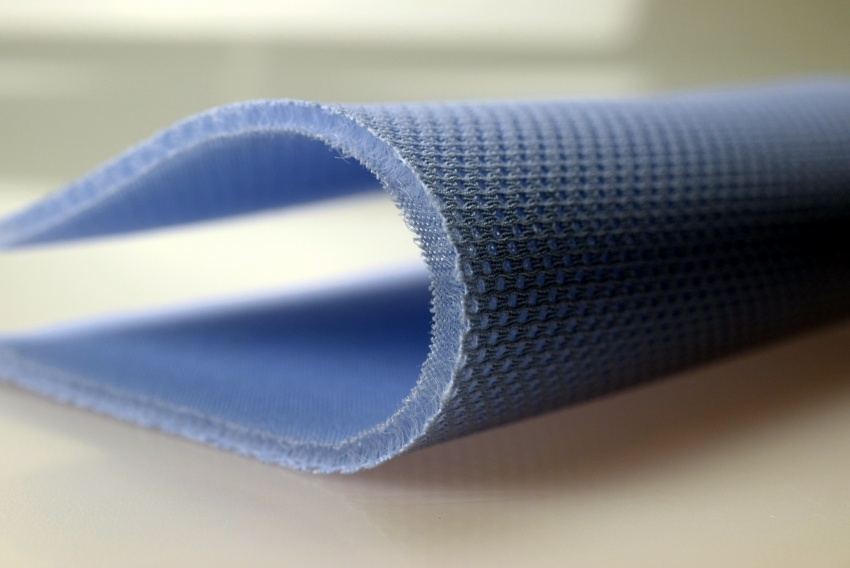
References:
Google Scholar
Image Source: https://www.bowistyl.pl/products/3d-spacer-fabric/3d-spacer-fabric/